Preparation method of ferrum-aluminum titanium carbide composite material
A composite material and titanium carbide technology, which is applied in the field of preparation of Fe3Al-TiC composite materials, can solve problems such as the reduction of plasticity at room temperature, and achieve the effect of improving hardness
- Summary
- Abstract
- Description
- Claims
- Application Information
AI Technical Summary
Problems solved by technology
Method used
Image
Examples
Embodiment 1
[0012] Weigh the mass percentage Fe 3 85% of Al powder and 15% of TiC powder were put into a sealed tank and dry mixed in a ball mill for 4 hours at a speed of 200r / min to obtain Fe 3 Composite powder of Al and 15% TiC, put the mixed composite powder into a graphite mold, place it in a vacuum hot-press sintering furnace for hot-press molding and sintering, and the vacuum degree is 1×10 -1 Pa, the heating rate is 10°C / min, the sintering temperature is 1250°C, the sintering pressure is 30MPa, and the sintering time is 30min. After the sintering is completed, cool to room temperature, take out the material, and obtain Fe 3 Al-15% TiC composite material, the material properties are given in the table below.
[0013]
Embodiment 2
[0015] Weigh the mass percentage Fe 3 75% of Al powder and 25% of TiC powder were put into a sealed tank and dry mixed in a ball mill for 6 hours at a speed of 200r / min to obtain Fe 3 Composite powder of Al and 25% TiC, put the mixed composite powder into a graphite mold, place it in a vacuum hot-press sintering furnace for hot-press forming and sintering, and the vacuum degree is 1×10 -1 Pa, the heating rate is 10°C / min, the sintering temperature is 1300°C, the sintering pressure is 35MPa, and the sintering time is 35min. After the sintering is completed, cool to room temperature, take out the material, and obtain Fe 3 Al-25% TiC bulk composite material, the material properties are given in the table below.
[0016]
Embodiment 3
[0018] Weigh the mass percentage Fe 3 65% of Al powder and 35% of TiC powder were put into a sealed tank and dry mixed in a ball mill for 6 hours at a speed of 250r / min to obtain Fe 3 Composite powder of Al and 35% TiC, put the mixed composite powder into a graphite mold, place it in a vacuum hot-press sintering furnace for hot-press forming and sintering, and the vacuum degree is 1×10 -2 Pa, the heating rate is 15°C / min, the sintering temperature is 1300°C, the sintering pressure is 40MPa, and the sintering time is 40min. After the sintering is completed, the furnace is cooled to room temperature, and the material is taken out to obtain Fe 3 Al-35%TiC bulk composite material, the material properties are given in the table below.
[0019]
PUM
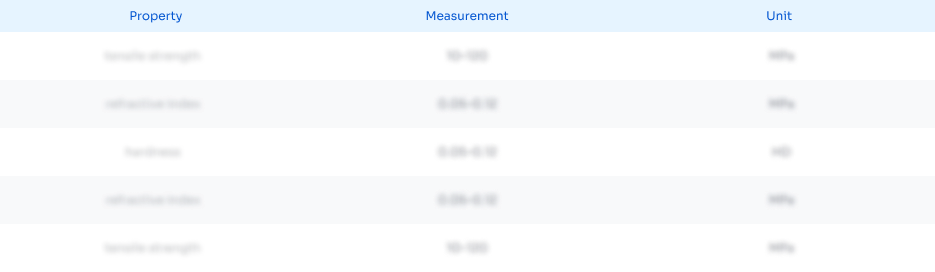
Abstract
Description
Claims
Application Information

- R&D
- Intellectual Property
- Life Sciences
- Materials
- Tech Scout
- Unparalleled Data Quality
- Higher Quality Content
- 60% Fewer Hallucinations
Browse by: Latest US Patents, China's latest patents, Technical Efficacy Thesaurus, Application Domain, Technology Topic, Popular Technical Reports.
© 2025 PatSnap. All rights reserved.Legal|Privacy policy|Modern Slavery Act Transparency Statement|Sitemap|About US| Contact US: help@patsnap.com