Novel process for synthesizing natural gas by methanation of coal gasification syngas
A chemical synthesis and natural gas technology, applied in the petroleum industry, gas fuel, fuel, etc., can solve the problems of harsh process conditions, low energy utilization rate, high production cost, etc., achieve low equipment cost, high conversion rate of raw material gas, and reduce use volume effect
- Summary
- Abstract
- Description
- Claims
- Application Information
AI Technical Summary
Problems solved by technology
Method used
Examples
Embodiment 1
[0026] Grind the catalyst to below 200 mesh, first put 300ml of paraffin or heat conduction oil in a 500ml autoclave, put in the ground Al 2 o 3 Ni catalyst as a carrier, first pass nitrogen gas and press to raise the temperature to 300 °C, after 2MPa, pass H 2 H / CO≥3:1 2 and CO gas, start to record the temperature change, and start to detect the tail gas after 1 hour of reaction. During the reaction, the temperature fluctuated in the range of 300–302 °C, and the CO conversion reached 98%.
[0027] Comparative test: Since the catalyst that is too fine will block the fixed bed layer, the catalyst is pressed into small balls and put into the fixed bed reactor. First, nitrogen gas is introduced to press and the temperature is raised to 300°C. After 2MPa, H 2 H / CO≥3:1 2 and CO gas, start to record the temperature change, and start to detect the tail gas after 1 hour of reaction. During the reaction, the temperature increased by 5 °C, and the CO conversion reached 97%.
Embodiment 2
[0029] Grind the catalyst to below 200 mesh, first put 300ml of paraffin or heat transfer oil in a 500ml autoclave, put the ground SiO 2 Ni catalyst as a carrier, first pass nitrogen gas and press to raise the temperature to 300 °C, after 2MPa, pass H 2 H / CO≥3:1 2 and CO gas, start to record the temperature change, and start to detect the tail gas after 1 hour of reaction. During the reaction, the temperature fluctuated in the range of 299–302 °C, and the CO conversion reached 97%.
[0030] Comparative test: SiO 2 The Ni catalyst as the carrier is pressed into small balls and placed in a fixed bed reactor. First, nitrogen gas is introduced to press and the temperature is raised to 300 ° C. After 2 MPa, H 2 H / CO≥3:1 2 and CO gas, start to record the temperature change, and start to detect the tail gas after 1 hour of reaction. During the reaction, the temperature fluctuated in the range of 300–305 °C, and the CO conversion reached 98%.
Embodiment 3
[0032] Grind the catalyst to below 200 mesh, put 300ml of paraffin or heat conduction oil in a 500ml autoclave first, put in the ground after using La as additive, Al 2 o 3 Ni catalyst as a carrier, first pass nitrogen gas and press to raise the temperature to 300 °C, after 2MPa, pass H 2 / C≥4:1H 2 And mixed gas containing C (CO, CO 2 ), began to record the temperature change, and started to detect the tail gas after 1 hour of reaction. During the reaction, the temperature fluctuated in the range of 298-301 °C, and the carbon conversion reached 96%.
[0033] Comparative test: La will be used as auxiliary agent, Al 2 o 3 The Ni catalyst as the carrier is pressed into small balls and placed in a fixed bed reactor. First, nitrogen gas is introduced to press and the temperature is raised to 300 ° C. After 2 MPa, H 2 / C≥4:1H 2 And mixed gas containing C (CO, CO 2 ), began to record the temperature change, and started to detect the tail gas after 1 hour of reaction. During th...
PUM
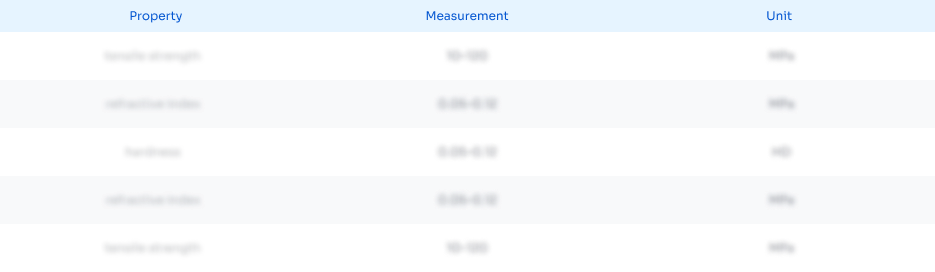
Abstract
Description
Claims
Application Information

- R&D Engineer
- R&D Manager
- IP Professional
- Industry Leading Data Capabilities
- Powerful AI technology
- Patent DNA Extraction
Browse by: Latest US Patents, China's latest patents, Technical Efficacy Thesaurus, Application Domain, Technology Topic, Popular Technical Reports.
© 2024 PatSnap. All rights reserved.Legal|Privacy policy|Modern Slavery Act Transparency Statement|Sitemap|About US| Contact US: help@patsnap.com