Design method of automatic control system for vapour-liquid consecutive reaction rectifying process
An automatic control system and serial reaction technology, applied in chemical/physics/physicochemical stationary reactors, fractionation, etc., can solve the difficulty of control system design and increase control accuracy requirements, and reduce the strong nonlinearity and coupling of closed-loop systems , less control degrees of freedom and other issues, to achieve the effect of ensuring long-term stable operation, increasing control accuracy and difficulty, and reducing control degrees of freedom
- Summary
- Abstract
- Description
- Claims
- Application Information
AI Technical Summary
Problems solved by technology
Method used
Image
Examples
Embodiment example
[0036] Implementation case: design case of automatic control system for benzene chlorination series reaction distillation process
[0037] Chlorinated benzene is often used in the manufacture of organic intermediates such as phenol, nitrochlorobenzene, aniline, and nitrophenol in the dye and pharmaceutical industries. The raw materials of the benzene chlorination reaction process are benzene and chlorine. The product is chlorinated benzene, and the by-product dichlorobenzene (mainly o-dichlorobenzene, p-dichlorobenzene) is obtained. The reaction formula is as follows:
[0038] The main reaction equation: (3)
[0039] Side reaction equation: (4)
[0040] Bourion has studied the kinetics of benzene chlorination by using ferric chloride as a catalyst, chlorine gas entering the liquid phase by bubbling, and obtained the kinetic equation of benzene chlorination as follows:
[0041] r 1 ...
PUM
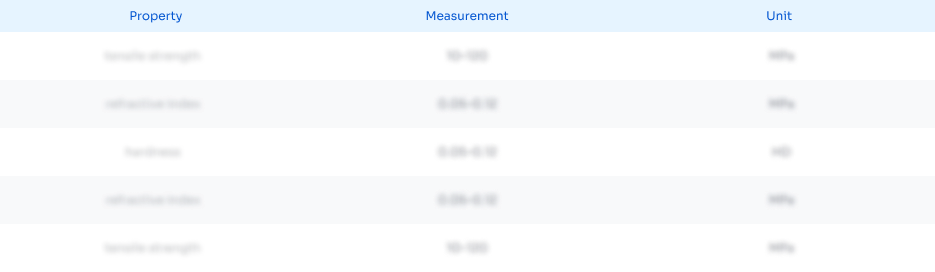
Abstract
Description
Claims
Application Information

- R&D
- Intellectual Property
- Life Sciences
- Materials
- Tech Scout
- Unparalleled Data Quality
- Higher Quality Content
- 60% Fewer Hallucinations
Browse by: Latest US Patents, China's latest patents, Technical Efficacy Thesaurus, Application Domain, Technology Topic, Popular Technical Reports.
© 2025 PatSnap. All rights reserved.Legal|Privacy policy|Modern Slavery Act Transparency Statement|Sitemap|About US| Contact US: help@patsnap.com