Production method of spray water paste
A production method and slurry technology, which is applied in the field of water spray slurry production, can solve the problems of high cost, large heat shrinkage, and complicated production methods, and achieve low environmental pollution, low odor concentration, and good heat shrinkage Effect
- Summary
- Abstract
- Description
- Claims
- Application Information
AI Technical Summary
Problems solved by technology
Method used
Image
Examples
Embodiment 1
[0021] Such as figure 1 Shown, the production method of water jet slurry comprises the following steps:
[0022] (1) For the first mixing, add 2 parts of acrylic acid, 3 parts of butyl acrylate, 4 parts of methyl methacrylate and 1 part of methacrylic acid into the polymerization tank in order by weight, stir and mix, and raise the temperature to 80°C;
[0023] (2) For the second mixing, add 1 part of water, 2 parts of emulsifier and 2 parts of initiator dropwise to the polymerization kettle of the step (1) by weight, and stir and mix. The dropping temperature is 80°C, and the dropping time is 5 hours, after the dropwise addition, keep warm for 4 hours;
[0024] (3), polymerization reaction, after the dropwise addition of the mixed solution in the step (2), heat preservation reaction for 4 hours;
[0025] (4) For the first cooling down, the temperature of the polymerization kettle is lowered to 60°C;
[0026] (5) For the third mixing, send the polymerized materials to the m...
Embodiment 2
[0033] The production method of water spray slurry, comprises the following steps:
[0034] (1) For the first mixing, add 3 parts of acrylic acid, 4 parts of butyl acrylate, 4 parts of methyl methacrylate and 2 parts of methacrylic acid into the polymerization kettle in order by weight, stir and mix, and heat up to 80°C;
[0035] (2) For the second mixing, add 2 parts of water, 3 parts of emulsifier and 3 parts of initiator dropwise into the polymerization kettle of the step (1) by weight and stir and mix. The dropping temperature is 83°C, and the dropping time is 5.5 hours, after the dropwise addition, keep warm for 4 hours;
[0036] (3), polymerization reaction, after the dropwise addition of the mixed solution in the step (2), heat preservation reaction for 4 hours;
[0037] (4) For the first cooling down, the temperature of the polymerization kettle is lowered to 63°C;
[0038] (5) Mixing for the third time, send the polymerized materials to the mixing tank, and add 0.2 ...
Embodiment 3
[0045] The production method of water spray slurry, comprises the following steps:
[0046] (1) For the first mixing, add 4 parts of acrylic acid, 5 parts of butyl acrylate, 6 parts of methyl methacrylate and 3 parts of methacrylic acid into the polymerization kettle in order to stir and mix according to parts by weight, and heat up to 80°C;
[0047] (2) For the second mixing, add 3 parts of water, 4 parts of emulsifier and 4 parts of initiator dropwise into the polymerization kettle of the step (1) by weight, and stir and mix. The dropping temperature is 85°C, and the dropping time is 6 hours, after the dropwise addition, keep warm for 4 hours;
[0048] (3), polymerization reaction, after the dropwise addition of the mixed solution in the step (2), heat preservation reaction for 4 hours;
[0049] (4) For the first cooling down, the temperature of the polymerization kettle is lowered to 65°C;
[0050] (5) Mixing for the third time, send the polymerized materials to the mixin...
PUM
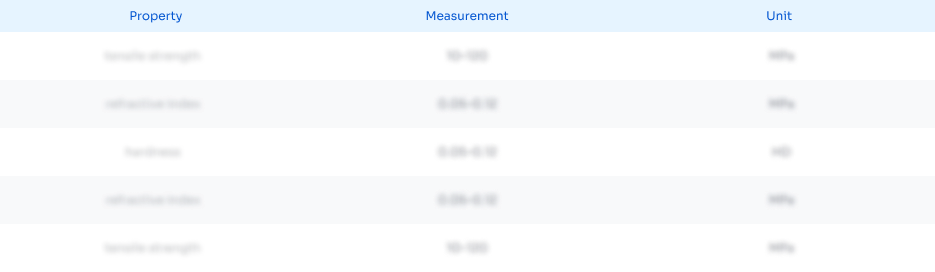
Abstract
Description
Claims
Application Information

- R&D
- Intellectual Property
- Life Sciences
- Materials
- Tech Scout
- Unparalleled Data Quality
- Higher Quality Content
- 60% Fewer Hallucinations
Browse by: Latest US Patents, China's latest patents, Technical Efficacy Thesaurus, Application Domain, Technology Topic, Popular Technical Reports.
© 2025 PatSnap. All rights reserved.Legal|Privacy policy|Modern Slavery Act Transparency Statement|Sitemap|About US| Contact US: help@patsnap.com