Black liquid bamboo charcoal and manufacturing method thereof
A manufacturing method and technology of black liquor bamboo, applied in special forms of dry distillation, solid fuel, biofuel, etc., can solve the problems of inability to use, large drying loss, waste of lignin resources, etc., and achieve large production capacity and short carbonization production cycle. , the effect of reducing stress
- Summary
- Abstract
- Description
- Claims
- Application Information
AI Technical Summary
Problems solved by technology
Method used
Examples
Embodiment
[0016] Take bamboo chips as raw material, weigh 75 kg per basket, add 10 kg of alkali lignin and mix evenly, invert it on the side pressure feeding system of a press with a specification of 2000mm*200mm*160mm, and then send it to the mold of the main pressure system after side pressure , under the action of a pressure of 50MPa, press and form, cover the template and lock it to fix it, stack it and send it into the carbonization furnace, close the kiln door and start heating, the temperature is controlled at 100-130°C, the time is 4 hours, and the top of the furnace is intermittently opened to exhaust The mouth releases water vapor until it finally closes, continue heating to 275°C for 5 hours, stop heating when it reaches 300°C, keep the temperature above 300°C for 7 hours, continue heating to 700°C for 5 hours for carbonization When finished, remove from the mold after cooling.
PUM
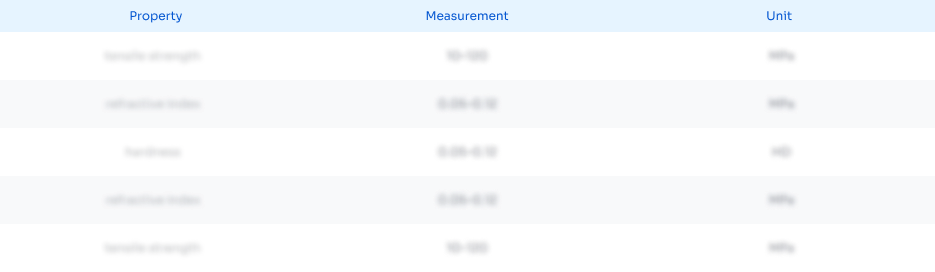
Abstract
Description
Claims
Application Information

- R&D
- Intellectual Property
- Life Sciences
- Materials
- Tech Scout
- Unparalleled Data Quality
- Higher Quality Content
- 60% Fewer Hallucinations
Browse by: Latest US Patents, China's latest patents, Technical Efficacy Thesaurus, Application Domain, Technology Topic, Popular Technical Reports.
© 2025 PatSnap. All rights reserved.Legal|Privacy policy|Modern Slavery Act Transparency Statement|Sitemap|About US| Contact US: help@patsnap.com