Structural error compensation control method of space phase modulation annular traveling wave ultrasonic motor
An ultrasonic motor and error compensation technology, applied in the direction of generators/motors, piezoelectric effect/electrostrictive or magnetostrictive motors, electrical components, etc., can solve problems such as space phase errors
- Summary
- Abstract
- Description
- Claims
- Application Information
AI Technical Summary
Problems solved by technology
Method used
Image
Examples
Embodiment Construction
[0054] The present invention will be further described below in conjunction with the accompanying drawings.
[0055] like figure 1 As shown, the motor includes an end cover 1, a bearing 1 2, a bearing 2 3, a rotating shaft 4, a rotor 5, a stator 6, a base 7, and piezoelectric ceramics. Except for the polarization division of piezoelectric ceramics, other structures, materials and assembly schemes of the motor are completely consistent with traditional ultrasonic motors. The piezoelectric ceramics of the motor are divided into A-zone piezoelectric ceramics 8 and B-zone piezoelectric ceramics 9 . like figure 2 As shown, when the motor is working, space traveling waves with nine wavelengths are distributed on the circumference of the stator. If each traveling wave wavelength is counted as a space phase of 2π, the entire circumference can be counted as a space phase of 18π. According to the clockwise direction, define the starting position of the piezoelectric ceramic 8 in the...
PUM
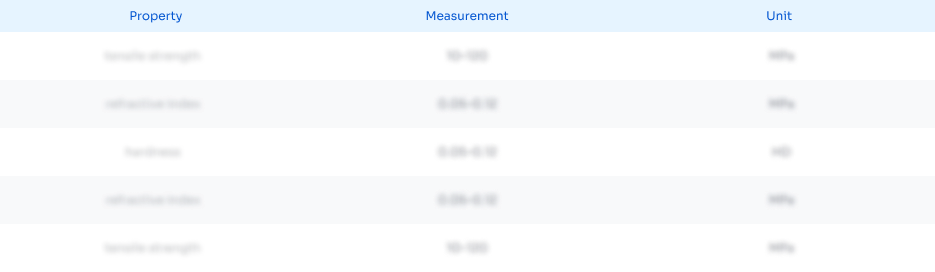
Abstract
Description
Claims
Application Information

- R&D
- Intellectual Property
- Life Sciences
- Materials
- Tech Scout
- Unparalleled Data Quality
- Higher Quality Content
- 60% Fewer Hallucinations
Browse by: Latest US Patents, China's latest patents, Technical Efficacy Thesaurus, Application Domain, Technology Topic, Popular Technical Reports.
© 2025 PatSnap. All rights reserved.Legal|Privacy policy|Modern Slavery Act Transparency Statement|Sitemap|About US| Contact US: help@patsnap.com