Preparation method of polyethylene flexible printing environment-friendly thin film
A polyethylene and film technology, applied in application, coating, ink and other directions, can solve the problems of difficult recycling of packaging bags, a large amount of waste, and difficult to degrade, and achieve the effect of low cost, strong industrial feasibility, and reduction of waste gas.
- Summary
- Abstract
- Description
- Claims
- Application Information
AI Technical Summary
Problems solved by technology
Method used
Image
Examples
Embodiment 1
[0021] 1) Mix polyethylene particles and polylactic acid evenly to obtain a mixture;
[0022] 2) Use a film blowing machine to heat and melt the mixture and blow it into a film;
[0023] 3) Use a slitting machine to slit the film;
[0024] 4) Coating the slit film, and the inks and solvents used in the coating process are water-soluble inks and solvents that do not contain toluene. The components of the ink are n-propanol, n-propyl acetate, ethyl Propanol and ethyl acetate, the weight percentages of n-propanol, n-propyl acetate, ethylene-propanol and ethyl acetate are 30% of n-propanol, 10% of n-propyl acetate, 1% of ethylene-propanol, and 1% of ethyl acetate , the composition of solvent has isopropanol, n-propyl acetate and butyl acetate, and the weight percentages of isopropanol, n-propyl acetate and butyl acetate are respectively isopropanol 55%, n-propyl acetate 25%, acetic acid Butyl fat 5%;
[0025] 5) Slitting the coated film;
[0026] 6) Use the bag making machine ...
Embodiment 2
[0029] 1) Mix polyethylene particles and polylactic acid evenly to obtain a mixture;
[0030] 2) Use a film blowing machine to heat and melt the mixture and blow it into a film;
[0031] 3) Use a slitting machine to slit the film;
[0032] 4) Coating the slit film, and the inks and solvents used in the coating process are water-soluble inks and solvents that do not contain toluene. The components of the ink are n-propanol, n-propyl acetate, ethyl Propanol and ethyl acetate, the weight percentages of n-propanol, n-propyl acetate, ethylene-propanol and ethyl acetate are 35% of n-propanol, 15% of n-propyl acetate, 6% of ethylene-propanol, and 5% of ethyl acetate , the composition of the solvent has isopropanol, n-propyl acetate and butyl acetate, and the weight percentages of isopropanol, n-propyl acetate and butyl acetate are respectively 60% of isopropanol, 30% of n-propyl acetate, acetic acid Butyl fat 10%;
[0033] 5) Slitting the coated film;
[0034] 6) Use the bag maki...
Embodiment 3
[0037] 1) Mix polyethylene particles and polylactic acid evenly to obtain a mixture;
[0038] 2) Use a film blowing machine to heat and melt the mixture and blow it into a film;
[0039] 3) Use a slitting machine to slit the film;
[0040] 4) Coating the slit film, and the inks and solvents used in the coating process are water-soluble inks and solvents that do not contain toluene. The components of the ink are n-propanol, n-propyl acetate, ethyl Propanol and ethyl acetate, the weight percentages of n-propanol, n-propyl acetate, ethylene-propanol and ethyl acetate are 40% of n-propanol, 20% of n-propyl acetate, 10% of ethylene-propanol, and 10% of ethyl acetate , the composition of the solvent has isopropanol, n-propyl acetate and butyl acetate, and the weight percentages of isopropanol, n-propyl acetate and butyl acetate are respectively 65% of isopropanol, 35% of n-propyl acetate, acetic acid Butyl fat 15%;
[0041] 5) Slitting the coated film;
[0042] 6) Use the bag ...
PUM
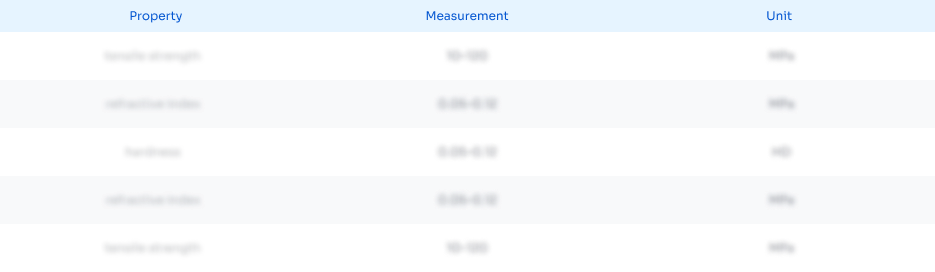
Abstract
Description
Claims
Application Information

- R&D
- Intellectual Property
- Life Sciences
- Materials
- Tech Scout
- Unparalleled Data Quality
- Higher Quality Content
- 60% Fewer Hallucinations
Browse by: Latest US Patents, China's latest patents, Technical Efficacy Thesaurus, Application Domain, Technology Topic, Popular Technical Reports.
© 2025 PatSnap. All rights reserved.Legal|Privacy policy|Modern Slavery Act Transparency Statement|Sitemap|About US| Contact US: help@patsnap.com