Method for preparing high-oriented gamma phase polyvinylidene fluoride PVDF thin film
A technology of polyvinylidene fluoride and vinylidene fluoride is applied in the field of preparing high-orientation γ-phase polyvinylidene fluoride PVDF film, which can solve the problems of lack of γ-crystal phase, high price, low crystallinity and melting point, etc.
- Summary
- Abstract
- Description
- Claims
- Application Information
AI Technical Summary
Problems solved by technology
Method used
Examples
Embodiment 1
[0015] A method for preparing highly oriented γ-phase polyvinylidene fluoride PVDF film, comprising the following steps:
[0016] 1) First, heat the polyvinylidene fluoride PVDF solution-cast film to 200°C for 10 minutes to eliminate the heat history, and then rapidly cool the polyvinylidene fluoride PVDF film to 170°C at a rate of 50°C / min;
[0017] 2) Utilize a polymethylsiloxane plate to apply 10 5 Pa pressure applies shear stress to the melt at a shear rate of 1.5m / s, and after standing at 170°C for 96 hours, the γ-phase PVDF film can be obtained, and the crystallization process of the melt in the shear stress field is observed under a polarizing microscope and the crystal structure after crystallization;
[0018] 3) Analyze the crystal structure and morphology of the columnar crystals after crystallization by infrared spectrum FTIR, scanning electron microscope SEM, transmission electron microscope TEM, differential scanning calorimeter DSC and other characterization met...
Embodiment 2
[0021] A method for preparing highly oriented γ-phase polyvinylidene fluoride PVDF film, comprising the following steps:
[0022] 1) First, heat the polyvinylidene fluoride PVDF solution-cast film to 205 °C for 10 minutes to eliminate the heat history, and then rapidly cool the polyvinylidene fluoride PVDF film to 165 °C at a rate of 50 °C / min;
[0023] 2) Utilize a polymethylsiloxane plate to apply 10 5 Pa pressure applies shear stress to the melt at a shear rate of 2.0m / s, and after standing at 165°C for 72 hours, the γ-phase PVDF film can be obtained, and the crystallization process of the melt in the shear stress field is observed under a polarizing microscope and the crystal structure after crystallization;
[0024] 3) Analyze the crystal structure and morphology of PVDF columnar crystals by means of FTIR infrared spectroscopy, scanning electron microscope SEM, transmission electron microscope TEM, and differential scanning calorimeter DSC to verify the crystal form of c...
Embodiment 3
[0027] A method for preparing highly oriented γ-phase polyvinylidene fluoride PVDF film, comprising the following steps:
[0028] 1) First, heat the polyvinylidene fluoride PVDF solution-cast film to 195°C for 10 minutes to eliminate the heat history, and then rapidly cool the polyvinylidene fluoride PVDF film to 160°C at a rate of 50°C / min;
[0029] 2) Utilize a polymethylsiloxane plate to apply 10 5 Pa pressure applies shear stress to the melt at a shear rate of 0.6m / s, and the α-phase PVDF film can be obtained after standing at 160°C for 48 hours. After 2 days of crystallization, continue annealing at 160°C for 120h to obtain α The γ-phase thin film after phase transition, observe the crystallization process of the melt in the shear stress field and the crystal structure after crystallization under a polarizing microscope;
[0030] 3) Analyze the crystal structure and morphology of the columnar crystals after crystallization by infrared spectrum FTIR, scanning electron mic...
PUM
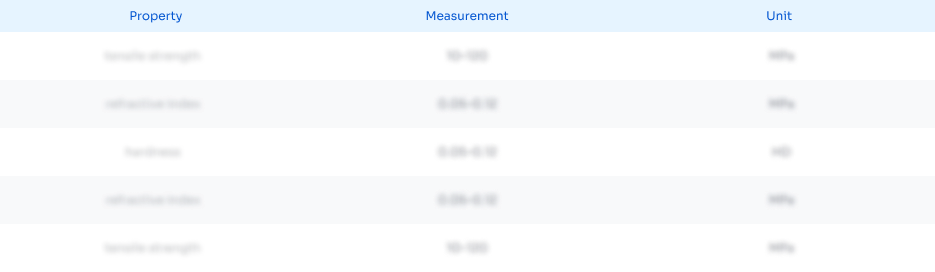
Abstract
Description
Claims
Application Information

- R&D
- Intellectual Property
- Life Sciences
- Materials
- Tech Scout
- Unparalleled Data Quality
- Higher Quality Content
- 60% Fewer Hallucinations
Browse by: Latest US Patents, China's latest patents, Technical Efficacy Thesaurus, Application Domain, Technology Topic, Popular Technical Reports.
© 2025 PatSnap. All rights reserved.Legal|Privacy policy|Modern Slavery Act Transparency Statement|Sitemap|About US| Contact US: help@patsnap.com