Bearing steel GCr15 production technology capable of preventing plugging of continuous casting water gap
A production process and continuous casting nozzle technology, which is applied in the field of bearing steel GCr15 production process, can solve the problems of low molten steel temperature returning to the furnace, increasing billet cost, continuous casting machine shutdown, etc., to reduce non-metallic inclusions and reduce billet cost , to avoid the effect of secondary oxidation
- Summary
- Abstract
- Description
- Claims
- Application Information
AI Technical Summary
Problems solved by technology
Method used
Examples
Embodiment Construction
[0017] In order to further understand the content of the invention, features and effects of the present invention, the following examples are given hereby, and the details are as follows:
[0018] A production process of bearing steel GCr15 that prevents the clogging of the continuous casting nozzle. The process route includes top-bottom re-blowing converter → LF refining furnace → VD vacuum degassing → Concast 6-machine 6-strand billet continuous casting, producing 6 furnaces in total.
[0019] (1) Converter process
[0020] Converter adopts double slag method for dephosphorization, high end carbon [C] ≥ 0.25%; before tapping, final slag basicity is required to be greater than 3.5, tapping temperature is 1630°C ~ 1650°C, ladle temperature is higher than 800°C, strict control of converter Lower slag, the amount of lower slag is less than 50mm thick.
[0021] furnace number End carbon [C]% Tapping temperature ℃ Final slag alkalinity 3106738 0.25 1635 3.62...
PUM
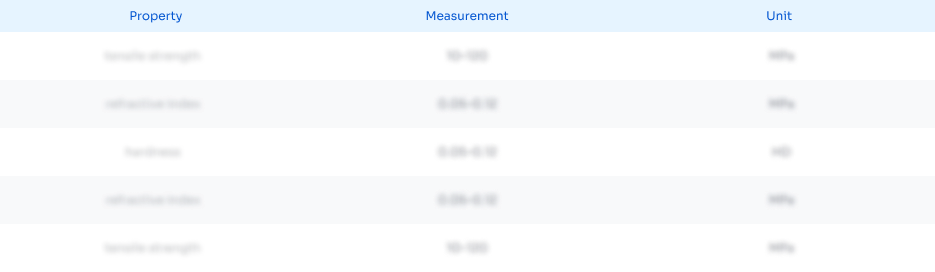
Abstract
Description
Claims
Application Information

- Generate Ideas
- Intellectual Property
- Life Sciences
- Materials
- Tech Scout
- Unparalleled Data Quality
- Higher Quality Content
- 60% Fewer Hallucinations
Browse by: Latest US Patents, China's latest patents, Technical Efficacy Thesaurus, Application Domain, Technology Topic, Popular Technical Reports.
© 2025 PatSnap. All rights reserved.Legal|Privacy policy|Modern Slavery Act Transparency Statement|Sitemap|About US| Contact US: help@patsnap.com