Method for preparing monodisperse crystal silicon dioxide spherical particles by coating carbon
A technology of silicon dioxide and spherical particles, applied in the direction of silicon dioxide, silicon oxide, etc., can solve the problem of not solving the production problem of monodisperse spherical crystalline silicon dioxide
- Summary
- Abstract
- Description
- Claims
- Application Information
AI Technical Summary
Problems solved by technology
Method used
Image
Examples
Embodiment 1
[0016] will pass The method is to mix 1g of 8nm silica colloid prepared from analytically pure tetraethoxysilane with 20mg of lithium chloride, 25ml of ethanol, and 5ml of hexane solution. Then, the mixture was atomized and sprayed into an aerosol reactor at 1100° C. with nitrogen gas, cooled, and black carbon-deposited core-shell silica particles with a particle size of 15 nm were collected. Treated at 850 °C for 4 hours under an argon atmosphere, the transmission electron microscope image shows that the silicon dioxide has been completely crystallized ( figure 1 ). XRD detection ( figure 2 ) found that there was no amorphous silica peak. The crystallized sample was treated with oxygen at 350° C. and 1 atmosphere for 10 hours to obtain ~7 nm non-agglomerated, monodisperse α-cristobalite nanoparticles.
Embodiment 2
[0018] pass 5g The method is to mix 150nm silicon dioxide prepared from analytically pure tetraethoxysilane with 100mg of lithium chloride, 10g of glucose, and 200ml of water. Pour this mixture into a polytetrafluoroethylene hydrothermal reaction kettle, stir it magnetically, raise the temperature to 180°C at 5°C / min, and keep the temperature constant for 8 hours. After cooling, it was settled by centrifugation, washed twice with water, dried at 150°C, and collected. Obtain the core-shell structure silica particle ( image 3 ). Treated at 900° C. for 8 hours under an argon atmosphere, transmission electron microscope images and XRD detection show that the silicon dioxide has been completely crystallized, and there is no amorphous silicon dioxide peak. The crystallized sample was treated with oxygen at 350° C. and 1 atmosphere for 10 hours to obtain non-agglomerated, monodisperse α-cristobalite particles of about 130 nm.
Embodiment 3
[0020] Pass 1g through The method is to mix 8nm silica colloid prepared from analytically pure tetraethoxysilane with 25ml ethanol and 5ml hexane solution evenly. Then, the mixture was sprayed into a 1100° C. aerosol reactor with nitrogen atomization, cooled, and collected to obtain black carbon-deposited core-shell structure silica particles with a diameter of 15 nm. Treat at 1000° C. for 12 hours under an argon atmosphere. XRD detection found that the silicon dioxide was not completely crystallized, and there were still amorphous silicon dioxide peaks.
PUM
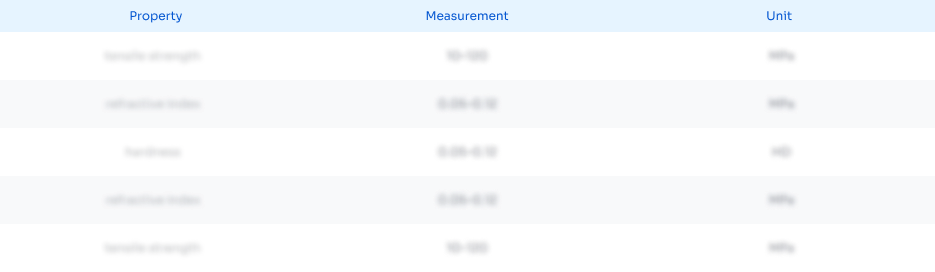
Abstract
Description
Claims
Application Information

- R&D
- Intellectual Property
- Life Sciences
- Materials
- Tech Scout
- Unparalleled Data Quality
- Higher Quality Content
- 60% Fewer Hallucinations
Browse by: Latest US Patents, China's latest patents, Technical Efficacy Thesaurus, Application Domain, Technology Topic, Popular Technical Reports.
© 2025 PatSnap. All rights reserved.Legal|Privacy policy|Modern Slavery Act Transparency Statement|Sitemap|About US| Contact US: help@patsnap.com