Chemical mechanical lapping device and system
A chemical machinery and grinding device technology, which is applied to grinding devices, abrasive surface adjustment devices, grinding machine tools, etc., can solve the problems that the stability of the polishing disc 14 is difficult to control, affect the uniform distribution of the grinding liquid, and the polishing disc 14 is cumbersome, etc. Slurry, easy to move, cost reduction effect
- Summary
- Abstract
- Description
- Claims
- Application Information
AI Technical Summary
Problems solved by technology
Method used
Image
Examples
Embodiment 1
[0059] combined reference image 3 and Figure 4 , the present embodiment provides a chemical mechanical polishing device, comprising:
[0060] A wafer support seat 26 is used to support the wafer 25 to be ground, and the surface to be ground of the wafer 25 is upward;
[0061] Grinding pad 24, is arranged on the top of described wafer supporting seat 26, and the grinding surface of described grinding pad 24 is downward and is opposite to the surface to be polished of described wafer 25, and the area of the grinding surface of described grinding pad 24 is smaller than described The area of the surface to be ground of the wafer 25;
[0062] The grinding pad fixing part 22 is arranged above the grinding pad 24 for fixing the grinding pad 24;
[0063] The shaft 21 is arranged above the polishing pad fixing part 22, and is used to drive the polishing pad fixing part 22 and the polishing pad 24 to rotate;
[0064] The raw material supply device 28 is arranged above the wafe...
Embodiment 2
[0083] refer to Figure 5 As shown, this embodiment provides a chemical mechanical grinding device, which is different from Embodiment 1 in that the raw material supply device is different.
[0084] The raw material supply device in this embodiment may include: a bearing cylinder 53 fixed on the upper surface of the grinding pad fixture 22; a grinding fluid supply pipe 48 arranged above the bearing cylinder 53 for supplying grinding fluid 29 ; the polishing pad fixing part 22 and the polishing pad 24 are provided with a plurality of through holes 50 passing through the polishing pad fixing part 22 and the polishing pad 24 .
[0085] In this embodiment, the grinding liquid 29 only needs to be sprayed on the grinding pad 24 , thereby further saving the grinding liquid 29 and further improving the uniformity of the distribution of the grinding liquid 29 .
[0086] Wherein, the carrying cylinder 53 may be a hollow cylinder with upper and lower openings.
[0087] Specifically, th...
PUM
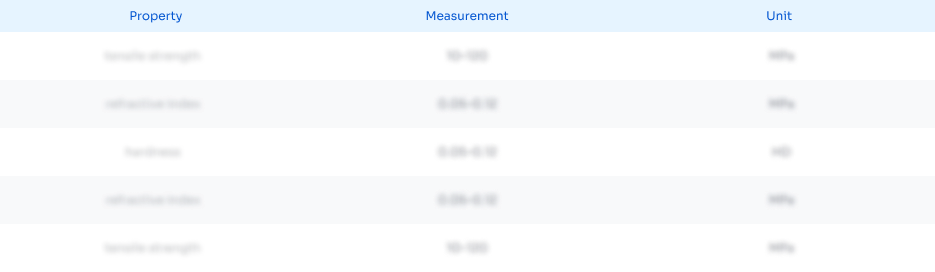
Abstract
Description
Claims
Application Information

- Generate Ideas
- Intellectual Property
- Life Sciences
- Materials
- Tech Scout
- Unparalleled Data Quality
- Higher Quality Content
- 60% Fewer Hallucinations
Browse by: Latest US Patents, China's latest patents, Technical Efficacy Thesaurus, Application Domain, Technology Topic, Popular Technical Reports.
© 2025 PatSnap. All rights reserved.Legal|Privacy policy|Modern Slavery Act Transparency Statement|Sitemap|About US| Contact US: help@patsnap.com