Power generating facility
A technology for power generation equipment and flash evaporator, which is applied in the field of steam turbine power generation systems, can solve problems such as unsatisfactory cost performance, and achieve the effects of suppressing operating costs, manufacturing costs, and equipment costs.
- Summary
- Abstract
- Description
- Claims
- Application Information
AI Technical Summary
Problems solved by technology
Method used
Image
Examples
Embodiment 1
[0031] figure 1 is a block diagram of the power generating equipment of the first embodiment, figure 2 is a block diagram of waste heat recovery power generation equipment applicable to this embodiment, image 3 It is a block diagram of the exhaust gas treatment facility to which the cement sintering facility of this embodiment is applied. In addition, in the drawings, the same reference numerals may be used to attach the same reference numerals to members showing the same functions, and explanations thereof may be omitted.
[0032] Such as figure 1 As shown, the power generation equipment of this embodiment represents that the power generation equipment of the present invention is applicable to image 3 An example of exhaust gas treatment equipment for a cement sintering plant is shown.
[0033] exist image 3 In the shown cement sintering equipment, the preheater (PH) 2 of the kiln 1 generates exhaust gas at 300 to 400°C, and the exhaust gas is used in the raw material...
Embodiment 2
[0063] Figure 4 is a block diagram of a power generation facility according to a second embodiment of the present invention. The thick line in the figure indicates the figure 2 Different parts of a prior art waste heat recovery power plant are shown.
[0064] In this embodiment, the same equipment as the constituent equipment of the first embodiment is used, but the piping for connecting the equipment is different. That is, when comparing the power generation equipment of this embodiment with the first embodiment, the relationship between the PH heat exchanger 61 for heat recovery from the low-temperature heat source of PH and the vacuum flasher 63 does not change, but the relationship between the low-temperature heat source of AQC Since the piping related to the AQC heat exchanger 62 for heat recovery is different from the piping related to the vacuum flasher 63 , the differences will be mainly described below in detail.
[0065] In the first embodiment, the return water...
Embodiment 3
[0069] Figure 5 is a block diagram of a power generation facility according to a third embodiment of the present invention.
[0070] This embodiment is based on installing a vacuum flash evaporator in existing power generation equipment to recover heat from a low-temperature heat source in the system that has not been available in the past to improve efficiency.
[0071] In the power plant of this embodiment, hot water and steam are generated by a heat source 71 such as a boiler and supplied to a gas-water separator 72 , and the high-pressure steam generated in the gas-water separator 72 is sent to a high-pressure stage of a steam turbine 75 . In addition, the water separated by the gas-water separator 72 is supplied to the flash evaporator 73 for flash evaporation to generate low-pressure steam and warm water, and the low-pressure steam is sent to the low-pressure stage of the steam turbine 75 .
[0072] The steam turbine 75 drives the generator 76 to generate electricity. ...
PUM
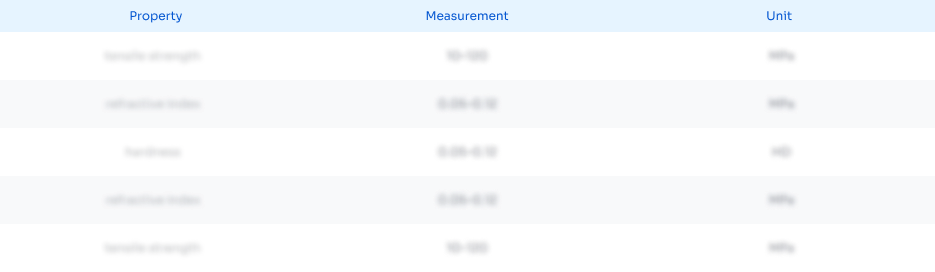
Abstract
Description
Claims
Application Information

- R&D
- Intellectual Property
- Life Sciences
- Materials
- Tech Scout
- Unparalleled Data Quality
- Higher Quality Content
- 60% Fewer Hallucinations
Browse by: Latest US Patents, China's latest patents, Technical Efficacy Thesaurus, Application Domain, Technology Topic, Popular Technical Reports.
© 2025 PatSnap. All rights reserved.Legal|Privacy policy|Modern Slavery Act Transparency Statement|Sitemap|About US| Contact US: help@patsnap.com