Monocrystalline silicon wafer precleaning liquid and cleaning method thereof
A single crystal silicon wafer, pre-cleaning technology, applied in cleaning methods and utensils, cleaning methods using liquids, chemical instruments and methods, etc. And other issues
- Summary
- Abstract
- Description
- Claims
- Application Information
AI Technical Summary
Problems solved by technology
Method used
Examples
Embodiment 1
[0021] Take 4.25 kg of hydrogen peroxide (concentration 30%), 0.24 kg of sodium hydroxide, add 95.51 kg of water to make 100 kg of cleaning solution, mix well, turn on the circulation and bubbling switch of the texturing machine, and turn off the bubbling after 5 minutes. Put the silicon wafers inserted into the flower basket into the pre-cleaning solution for single crystal silicon wafers mixed uniformly, at a temperature of 55°C, use ultrasonic cleaning for 60 seconds, after ultrasonic cleaning, rinse with deionized water for 1 minute at 60°C Finally, the silicon wafers were removed and dried after rinsing with deionized water.
Embodiment 2
[0023] Take 3 kg of hydrogen peroxide (concentration 30%), 0.2 kg of sodium hydroxide, add 96.8 kg of water to make 100 kg of cleaning solution, mix well, turn on the cycle and bubbling switch of the texturing machine, and turn off the bubbling after 3 minutes. Put the silicon wafers inserted into the flower basket into the pre-cleaning solution for single crystal silicon wafers mixed uniformly, at a temperature of 65°C, use ultrasonic cleaning for 300 seconds, after ultrasonic cleaning, rinse with deionized water for 1 minute at 60°C Finally, the silicon wafers were removed and dried after rinsing with deionized water.
Embodiment 3
[0025] Take 7 kg of hydrogen peroxide (concentration 30%), 1 kg of sodium hydroxide, add 92 kg of water to make 100 kg of cleaning solution, mix well, turn on the cycle and bubbling switch of the texturing machine, and turn off the bubbling after 4 minutes. Put the silicon wafers inserted into the flower basket into the pre-cleaning solution for single crystal silicon wafers mixed uniformly, at a temperature of 80°C, use ultrasonic cleaning for 600 seconds, after ultrasonic cleaning, rinse with deionized water for 1 minute at 60°C Finally, the silicon wafers were removed and dried after rinsing with deionized water.
PUM
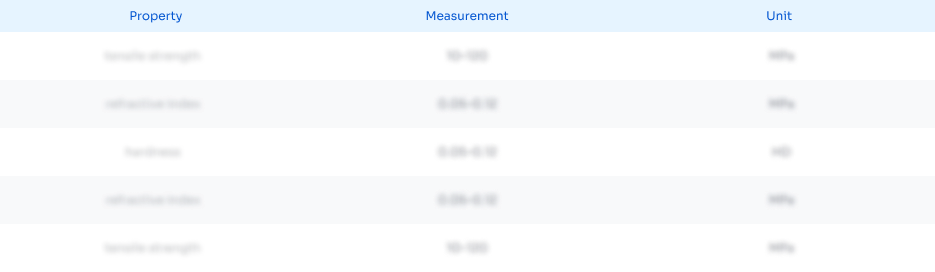
Abstract
Description
Claims
Application Information

- R&D
- Intellectual Property
- Life Sciences
- Materials
- Tech Scout
- Unparalleled Data Quality
- Higher Quality Content
- 60% Fewer Hallucinations
Browse by: Latest US Patents, China's latest patents, Technical Efficacy Thesaurus, Application Domain, Technology Topic, Popular Technical Reports.
© 2025 PatSnap. All rights reserved.Legal|Privacy policy|Modern Slavery Act Transparency Statement|Sitemap|About US| Contact US: help@patsnap.com