Sintering method of abrasion resisting abrasive particles
A sintering method and abrasive grain technology, applied in chemical instruments and methods, other chemical processes, etc., can solve the problems of affecting the grinding effect, clogging of abrasive tools, high temperature, etc., and achieve low manufacturing cost, high grinding efficiency, and good wear resistance performance effect
- Summary
- Abstract
- Description
- Claims
- Application Information
AI Technical Summary
Problems solved by technology
Method used
Image
Examples
Embodiment 1
[0023] Embodiments 1-9 are specific embodiments of the sintering method of wear-resistant abrasive grains of the present invention, and embodiment 1 is the best embodiment.
[0024] Example 1
[0025] 1) Using hot air drying equipment, mix according to the ratio of 10 parts by weight of sodium silicate, 5 parts of sodium carbonate, 25 parts of slag powder and 100 parts of alumina abrasive with a particle size of 80#, and dissolve in 120 parts of ethylene glycol after mixing evenly Diethyl ether solvent, and add 4 parts of ethylenediamine as a catalyst for mixing, constant temperature heating, keep the temperature at 35~45°C;
[0026] 2) Mix to semi-gel state, mix 0.5 part of template agent with cetyltrimethylammonium bromide (CTAB): ethylenediamine=1:2 by mass ratio, add template agent to semi-gel state In the molten material; after stirring evenly, sintering, the sintering temperature is 300~400°C, and the sintering time is 8 hours; after sintering, it is quickly annealed ...
Embodiment 2
[0028] 1) Using hot air drying equipment, mix according to the ratio of 15 parts by weight of lithium silicate, 8 parts of potassium bicarbonate, 30 parts of modified dolomite powder and 100 parts of silicon carbide abrasive with a particle size of 240#, and dissolve them in 140 Parts of ethylene glycol ether solvent, and add 5 parts of ethylenediamine as a catalyst for mixing, constant temperature heating, keep the temperature at 40~50°C;
[0029] 2) Mix to semi-gel state, mix 0.9 parts of template agent with cetyltrimethylammonium bromide (CTAB):ethylenediamine=1:2.5 by mass ratio, add template agent to semi-gel state In the molten material; after stirring evenly, sintering, the sintering temperature is 300~400°C, and the sintering time is 9 hours; after sintering, anneal and cool down quickly, crush, sieve, and separate the 20# abrasive grains.
Embodiment 3
[0031] 1) Using hot air drying equipment, mix according to the ratio of 5 parts by weight of aluminum dihydrogen phosphate, 6 parts of sodium hydroxide, 10 parts of modified kaolin and 60 parts of calcined alumina with a particle size of 1200#, and dissolve in 100 parts after mixing evenly Part of ethylene glycol ether solvent, and add 2 parts of ethylenediamine as a catalyst for mixing, constant temperature heating, keep the temperature at 30~40°C;
[0032] 2) Mix to semi-gel state, mix 0.8 parts of template agent with cetyltrimethylammonium bromide (CTAB): ethylenediamine=1:2.5 by mass ratio, add template agent to semi-gel state In the molten material; after stirring evenly, sintering, the sintering temperature is 300~400°C, and the sintering time is 6 hours; after sintering, it is quickly annealed and cooled, crushed, sieved, and 16# abrasive grains are separated.
PUM
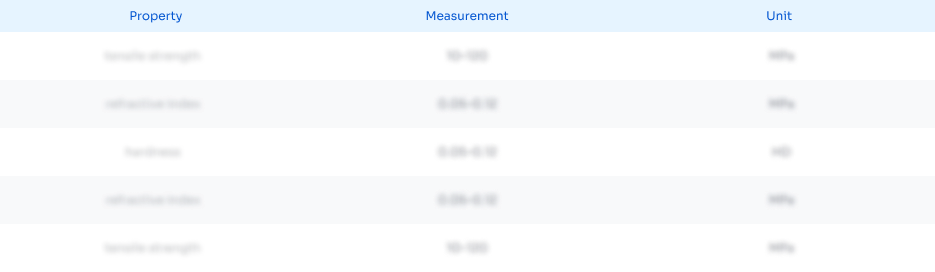
Abstract
Description
Claims
Application Information

- Generate Ideas
- Intellectual Property
- Life Sciences
- Materials
- Tech Scout
- Unparalleled Data Quality
- Higher Quality Content
- 60% Fewer Hallucinations
Browse by: Latest US Patents, China's latest patents, Technical Efficacy Thesaurus, Application Domain, Technology Topic, Popular Technical Reports.
© 2025 PatSnap. All rights reserved.Legal|Privacy policy|Modern Slavery Act Transparency Statement|Sitemap|About US| Contact US: help@patsnap.com