Method for removing magnesium from ultralow-quality phosphate rock and producing magnesium hydroxide
A technology of magnesium hydroxide and phosphate rock, applied in magnesium hydroxide and other directions, to achieve the effects of low one-time investment cost, high yield and reduced loss
- Summary
- Abstract
- Description
- Claims
- Application Information
AI Technical Summary
Problems solved by technology
Method used
Image
Examples
Embodiment 1
[0032] Take ultra-low-grade phosphate rock (P 2 o 5 ≤28%, MgO≥3%, MgO / P 2 o 5 ≥10%). Grind phosphate rock to obtain phosphate rock powder with a fineness of 60 mesh; add sulfurous acid with a concentration of 5% and sulfuric acid with a concentration of 5% into a solution of fluosilicic acid with a concentration of 17%, and the mass ratio of the addition is sulfurous acid : sulfuric acid: fluosilicic acid = 1: 1.2: 1.3, stir evenly to obtain a mixed acid demagnesizing agent; add phosphate rock powder to the mixed acid demagnesizing agent, heat up to 30°C, stir at a rate of 300r / min, and react for 10 minutes , the reaction is completed when the reaction solution pH=3; after the reaction is completed, the solution is separated from the solid phase by filtration while it is hot, and the solution is a solution containing magnesium salt; the solid phase is washed with distilled water until the washing water is neutral, and the obtained solid Drying, that is, phosphate ore conce...
Embodiment 2
[0034] Take ultra-low-grade phosphate rock (P2 o 5 ≤28%, MgO≥3%, MgO / P 2 o 5 ≥10%). Grind phosphate rock to obtain phosphate rock powder with a fineness of 80 meshes; add sulfurous acid with a concentration of 10% and sulfuric acid with a concentration of 10% to a solution of fluosilicic acid with a concentration of 34%, and the added mass ratio is sulfurous acid : Sulfuric acid: Fluosilicic acid = 1: 1.2: 1.3, stir evenly to obtain a mixed acid demagnesizing agent; add phosphate rock powder to the mixed acid demagnesizing agent, heat up to 45°C, stir at a rate of 325r / min, and react for 30 minutes , the reaction is completed when the reaction solution pH=4; after the reaction is completed, the solution is separated from the solid phase by filtration while it is hot, and the solution is a solution containing magnesium salt; the solid phase is washed with distilled water until the washing water is neutral, and the obtained solid Drying, that is, phosphate ore concentrate; mi...
Embodiment 3
[0036] Take ultra-low-grade phosphate rock (P 2 o 5 ≤28%, MgO≥3%, MgO / P 2 o 5 ≥10%). Grind phosphate rock to obtain phosphate rock powder with a fineness of 100 mesh; add sulfurous acid with a concentration of 20% and sulfuric acid with a concentration of 20% to a solution of fluosilicic acid with a concentration of 51%, and the added mass ratio is sulfurous acid : sulfuric acid: fluosilicic acid = 1: 1.2: 1.3, stir evenly to obtain a mixed acid demagnesizing agent; add phosphate rock powder to the mixed acid demagnesizing agent, heat up to 60°C, stir at a rate of 350r / min, and react for 60 minutes , the reaction is completed when the reaction solution pH=6; after the reaction is completed, the solution is separated from the solid phase by filtration while it is hot, and the solution is a solution containing magnesium salt; the solid phase is washed with distilled water until the washing water is neutral, and the obtained solid Drying, that is, phosphate ore concentrate; m...
PUM
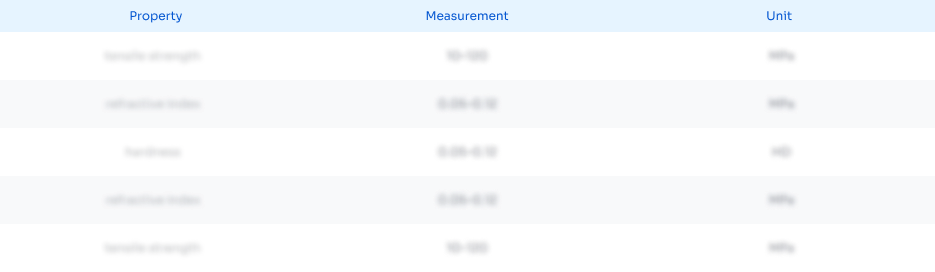
Abstract
Description
Claims
Application Information

- R&D
- Intellectual Property
- Life Sciences
- Materials
- Tech Scout
- Unparalleled Data Quality
- Higher Quality Content
- 60% Fewer Hallucinations
Browse by: Latest US Patents, China's latest patents, Technical Efficacy Thesaurus, Application Domain, Technology Topic, Popular Technical Reports.
© 2025 PatSnap. All rights reserved.Legal|Privacy policy|Modern Slavery Act Transparency Statement|Sitemap|About US| Contact US: help@patsnap.com