Preparation method of anti-corrosion coating on the surface of 310/316 stainless steel fiber sintered felt
A technology for sintering felt and steel fibers, applied in fiber processing, separation methods, chemical instruments and methods, etc., can solve the problems of easy corrosion and short service life, and achieve improved corrosion resistance, good air permeability, and high filtration accuracy. Effect
- Summary
- Abstract
- Description
- Claims
- Application Information
AI Technical Summary
Problems solved by technology
Method used
Examples
preparation Embodiment 1
[0030] Prepare an aluminum sol coating solution with a solid content of 20%.
[0031] The FeCrAl fiber sintered felt was immersed in the above-prepared aluminum sol coating solution at a rate of 20cm / min, and then lifted out of the solution at a rate of 20cm / min. The lifting instrument adopts PZ-SD-04 of Shanghai Renzhong Instrument Electric Co., Ltd. Frequency conversion speed power supply.
[0032] Place the above conventional dissolving FeCrAl fiber sintered felt in a vacuum container to evacuate to drive out bubbles in the coating for 20 minutes. The instrument uses a 2XZ-type rotary vane vacuum pump from Shanghai Vacuum Pump Factory Co., Ltd.
[0033] Put the FeCrAl fiber sintered felt treated by the above method into a muffle furnace, heat up to 650℃, keep it for 2 hours, and form a stable γ-Al on the surface 2 O 3 membrane. The instrument used Nabertherm Industrial Furnaos Ltd, CO's LH60 / 13 muffle furnace.
preparation Embodiment 2
[0035] Prepare an aluminum sol coating solution with a solid content of 23%.
[0036] The FeCrAl fiber sintered felt was immersed in the above-prepared aluminum sol coating solution at a rate of 30cm / min, and then lifted out of the solution at a rate of 30cm / min. The lifting instrument was PZ-SD-04 made by Shanghai Renzhong Instrument Electric Co., Ltd. Frequency conversion speed power supply.
[0037] Place the above-mentioned conventionally-dissolved FeCrAl fiber sintered felt in a vacuum container to evacuate to drive out bubbles in the coating for 25 minutes. The instrument uses a 2XZ-type rotary vane vacuum pump from Shanghai Vacuum Pump Factory Co., Ltd.
[0038] Put the FeCrAl fiber sintered felt treated by the above method into a muffle furnace, heat up to 630°C, keep it for 2.5 hours, and form a stable γ-Al on the surface 2 O 3 membrane. The instrument used Nabertherm Industrial Furnaos Ltd, CO's LH60 / 13 muffle furnace.
preparation Embodiment 3
[0040] Prepare an aluminum sol coating solution with a solid content of 25%.
[0041] The FeCrAl fiber sintered felt was immersed in the above-prepared aluminum sol coating solution at a rate of 40cm / min, and then lifted out of the solution at a rate of 40cm / min. The lifting instrument adopts PZ-SD-04 of Shanghai Renzhong Instrument Electric Co., Ltd. Frequency conversion speed power supply.
[0042] Place the above-mentioned conventional dissolving FeCrAl fiber sintered felt in a vacuum container to evacuate to drive out bubbles in the coating for 30 minutes. The instrument uses a 2XZ-type rotary vane vacuum pump from Shanghai Vacuum Pump Factory Co., Ltd.
[0043] Put the FeCrAl fiber sintered felt treated by the above method into a muffle furnace, raise it to 650℃ at a certain heating rate, and keep it for 3 hours to form a stable γ-Al on the surface 2 O 3 membrane. The instrument used Nabertherm Industrial Furnaos Ltd, CO's LH60 / 13 muffle furnace.
[0044] Γ-Al mentioned above 2 ...
PUM
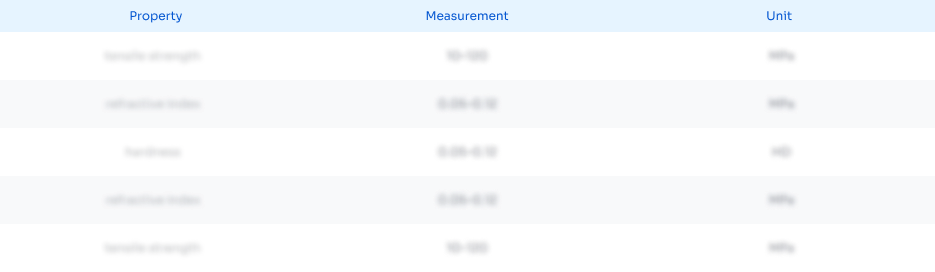
Abstract
Description
Claims
Application Information

- R&D Engineer
- R&D Manager
- IP Professional
- Industry Leading Data Capabilities
- Powerful AI technology
- Patent DNA Extraction
Browse by: Latest US Patents, China's latest patents, Technical Efficacy Thesaurus, Application Domain, Technology Topic, Popular Technical Reports.
© 2024 PatSnap. All rights reserved.Legal|Privacy policy|Modern Slavery Act Transparency Statement|Sitemap|About US| Contact US: help@patsnap.com