Dephosphorizing and steelmaking method of medium-high-phosphorous semisteel by top-blown converter
A technology for blowing converters, medium and high phosphorus, applied in the direction of manufacturing converters, etc., can solve the problems of insufficient reaction space of iron ladle, difficult to combine molten iron phosphorus, large amount of slag, etc., to expand low-cost reserves, reduce lime consumption, and reduce production costs. Effect
- Summary
- Abstract
- Description
- Claims
- Application Information
AI Technical Summary
Problems solved by technology
Method used
Examples
Embodiment 1
[0031] 1. Remaining slag and splashing slag: add 3.2kg / t after tapping the furnace steel 钢 Magnesite ball slag splashing for 3.5min, slag splashing pressure 0.85MPa, slag splashing gun position 800mm-1400mm, lime 16.5kg / t added to the bottom of the furnace before the semi-steel is put into the furnace 钢 , then add 63t of semi-steel, and add 5.56kg / t of hot casting slag together with the semi-steel 钢 Entering the converter to be smelted, the carbon content of semi-steel is 2.98%, and the phosphorus content is 0.375%;
[0032] 2. Add semi-steel slagging agent 4.76kg / t before blowing 钢 , when the gun blowing slag material starts to melt, start to add lime in small quantities and in multiple batches, and the total amount of lime added is 13.49kg / t 钢 , (control the slag basicity in the early stage at 2.8-4.0), the oxygen lance position is controlled at 1200mm when blowing starts, and the lance position is controlled at 1400mm from the liquid surface after 2.5 minutes of blowing (...
Embodiment 2
[0036] 1. Remaining slag and splashing slag: add 3.6kg / t after the steel is tapped from the upper furnace 钢 Magnesite ball slag splashing for 2.8min, slag splashing pressure 0.85MPa, slag splashing gun position 850mm-1200mm, lime 16.7kg / t added to the bottom of the furnace before the semi-steel is put into the furnace 钢 , and then add 63.5t of semi-steel, and add 5.04kg / t of hot casting slag together with the semi-steel 钢 Entering the converter to be smelted, the carbon content of semi-steel is 3.49%, and the phosphorus content is 0.466%.
[0037] 2. Add semi-steel slagging agent 4.72kg / t before blowing 钢 , when the slag blowing slag material starts to melt, a small amount of lime is added in multiple batches, and the total amount of lime added is 13.38kg / t 钢 , (control the slag basicity in the early stage at 2.8-4.0), the oxygen lance position is controlled at 1200mm when blowing starts, and the lance position is controlled at 1400mm from the liquid surface after 2.4 minute...
Embodiment 3
[0041] 1. Remaining slag and splashing slag: add 3.4kg / t after tapping the upper furnace steel 钢 Magnesite ball slag splashing for 3.2min, slag splashing pressure 0.85MPa, slag splashing gun position 800mm-1400mm, lime 16.32kg / t added to the bottom of the furnace before the semi-steel is put into the furnace 钢 , then add 62.8t of semi-steel, and add 5.89kg / t of hot casting slag together with the semi-steel 钢 Entering the converter to be smelted, the carbon content of semi-steel is 3.53%, and the phosphorus content is 0.616%.
[0042] 2. Add semi-steel slagging agent 4.78kg / t before blowing 钢 , when the slag blowing slag material starts to melt, a small amount of lime is added in multiple batches, and the total amount of lime added is 14.81kg / t 钢 , (control the slag basicity in the early stage at 2.8-4.0), the oxygen lance position is controlled at 1200mm when blowing starts, and the lance position is controlled at 1400mm from the liquid surface after 2 minutes of blowing (p...
PUM
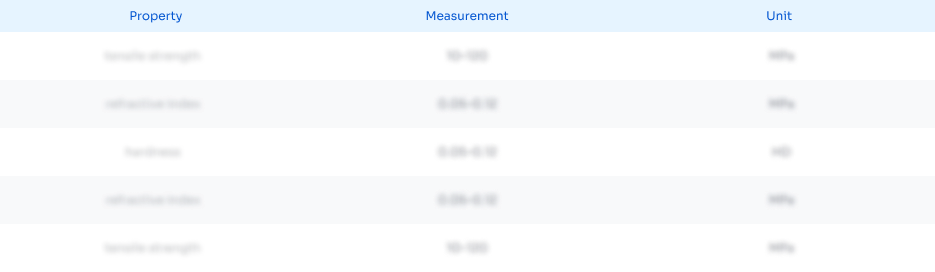
Abstract
Description
Claims
Application Information

- R&D
- Intellectual Property
- Life Sciences
- Materials
- Tech Scout
- Unparalleled Data Quality
- Higher Quality Content
- 60% Fewer Hallucinations
Browse by: Latest US Patents, China's latest patents, Technical Efficacy Thesaurus, Application Domain, Technology Topic, Popular Technical Reports.
© 2025 PatSnap. All rights reserved.Legal|Privacy policy|Modern Slavery Act Transparency Statement|Sitemap|About US| Contact US: help@patsnap.com