Combined hydrogenation method of producing chemical materials
A chemical raw material and hydrocracking technology, which is applied in the fields of hydrotreating process, petroleum industry, and hydrocarbon oil treatment, and can solve the problem of not mentioning the combination of diesel hydrotreating/upgrading unit and not mentioning the specific distillation of middle distillate oil. process and other issues, to achieve the effect of increased yield, small volume and good selectivity
- Summary
- Abstract
- Description
- Claims
- Application Information
AI Technical Summary
Problems solved by technology
Method used
Image
Examples
Embodiment 1
[0052] In the wax oil hydrocracking unit, the reaction pressure is 13.0MPa, the reaction temperature of the hydrofinishing reactor is 370°C, and the volume space velocity is 1.0h -1 ; The reaction temperature of the first hydrocracking reactor is 366°C, and the volume space velocity is 1.4h -1 ; The temperature of the second hydrocracking reactor in the diesel hydrotreating unit is 405°C and the volume space velocity is 10.0h -1 1. Under the reaction condition of reaction pressure 8.0MPa, with the method provided by the invention, adopt raw material A to carry out experiment. Among them, 100% of the diesel fraction (175-320° C.) obtained from the first hydrocracking reactor was re-refined to the second hydrocracking reactor under pressure. The distribution of the test products and the properties of the main products are shown in Table 2.
[0053] As can be seen from Table 2, under the condition of > 350 DEG C conversion rate is about 57%, the productive rate of heavy naphtha ...
Embodiment 2
[0055] Adopt the method provided by the present invention, control > 350 ℃ conversion rate about 79%, under reaction pressure 13.0MPa, hydrogenation reactor reaction temperature 370 ℃, volume space velocity 1.0h -1 ; The reaction temperature of the first hydrocracking reactor is 376°C, and the volume space velocity is 1.4h -1 Under the condition, with the method provided by the invention, adopt raw material A to carry out experiment. 50% of the 175-320°C diesel fraction is recycled to the inlet of the second hydrocracking reactor, the reaction temperature of the second hydrocracking reactor is 385°C, and the volume space velocity is 4.5h -1 . The distribution of test products and the properties of main products are shown in Table 3. It can be seen from Table 3 that under the condition of >350°C conversion rate of about 79%, the yield of heavy naphtha obtained by back refining can reach 39.1%, the selectivity of heavy naphtha is 84.6%, and the aromatic potential is 64.0%. In ...
Embodiment 3
[0057] Adopt the method provided by the present invention, control > 350 ℃ conversion rate about 78%, under reaction pressure 13.0MPa, hydrogenation reactor reaction temperature 370 ℃, volumetric space velocity 1.0h -1 ; The reaction temperature of the first hydrocracking reactor is 376°C, and the volume space velocity is 1.4h -1 Under the condition, with the method provided by the invention, adopt raw material A to carry out experiment. Among them, 100% of the 175-320°C diesel fraction is recycled to the inlet of the second hydrocracking reactor, the reaction temperature of the second hydrocracking reactor is 406°C, and the volume space velocity is 9.0h-1 , product distribution and product quality data of heavy naphtha are listed in Table 4. It can be seen from Table 4 that under the condition of >350°C with a conversion rate of about 78%, the yield of heavy naphtha obtained by back refining can reach 48.15%, the selectivity of heavy naphtha is 85.1%, and the aromatic potenti...
PUM
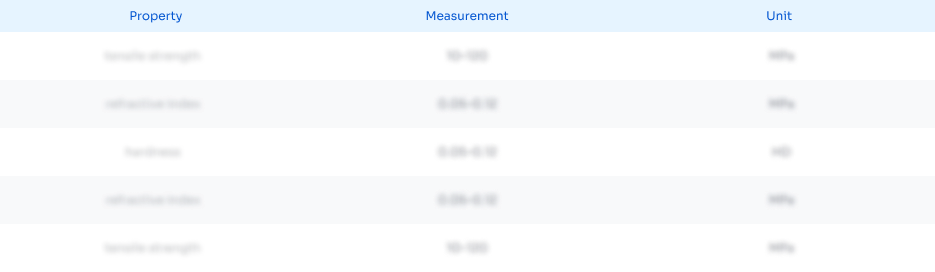
Abstract
Description
Claims
Application Information

- R&D
- Intellectual Property
- Life Sciences
- Materials
- Tech Scout
- Unparalleled Data Quality
- Higher Quality Content
- 60% Fewer Hallucinations
Browse by: Latest US Patents, China's latest patents, Technical Efficacy Thesaurus, Application Domain, Technology Topic, Popular Technical Reports.
© 2025 PatSnap. All rights reserved.Legal|Privacy policy|Modern Slavery Act Transparency Statement|Sitemap|About US| Contact US: help@patsnap.com