Secondary coupled modified mineral powder filling material and preparation process thereof
A technology of mineral powder and mineral filler, which is applied in the direction of fibrous filler, dyed organic silicon compound treatment, dyed low molecular organic compound treatment, etc., can solve problems such as difficulties, and achieve improved reinforcement performance, good compatibility, and adhesion The effect of high branch efficiency
- Summary
- Abstract
- Description
- Claims
- Application Information
AI Technical Summary
Problems solved by technology
Method used
Image
Examples
Embodiment 1
[0021] Preparation of modified montmorillonite powder mineral filler:
[0022] Add 20 kg of a mixture of acetone and ethyl acetate with a volume ratio of 1:1 in a 50L autoclave, then add 1.0 kg of silane coupling agent, and stir to form a uniform solution. When the stirring speed is lower than 25rpm, add 10kg of montmorillonite mineral content 92%, specific surface area 105m 2 / g powder, airtight the reactor, energize and heat to 60℃, control the stirring speed to 1500rpm, stir for 1h, and ultrasonically disperse during 20min. After standing to cool, add 1.0kg of 1,4-pentadiene, continue to seal, keep keeping the temperature at 90°C, and stir for 2h under the condition of 1500rpm, during which ultrasonic dispersion is 20min. After the solid-liquid separation after cooling, the solid-phase part is dried at 106°C, pulverized by jet mill, and sealed and stored to obtain secondary modified montmorillonite mineral powder.
[0023] Use the powder to fill EPDM rubber, the formula is base...
Embodiment 2
[0025] Preparation of modified sepiolite mineral powder filler:
[0026] Add 20kg of n-butanol to a 50L autoclave, then add 0.1kg of silane coupling agent and 0.1kg of titanate coupling agent, and stir to form a uniform solution. When the stirring speed is lower than 25rpm, add 10kg of sepiolite with a mineral content of 95% and a specific surface area of 126m 2 / g powder, airtight the reactor, energize and heat to 90°C, control the stirring speed to 1500rpm, stir for 1h, and ultrasonically disperse for 20min during this period. After standing to cool, add 0.2kg of acrylonitrile, continue to seal, keep the temperature at 120°C, and stir at 1500rpm for 2h, during which time it is ultrasonically dispersed for 20min. After the solid-liquid separation after cooling, the solid-phase part is dried at 120°C, pulverized by jet mill, and sealed and stored to obtain the sepiolite mineral powder modified by secondary coupling synergistically.
[0027] When using this powder to fill nitrile...
Embodiment 3
[0029] Preparation of modified attapulgite mineral powder filler:
[0030] Add 20 kg of a mixture of isopropanol and toluene with a volume ratio of 1:1 in a 50L autoclave, then add 1.0 kg of silane coupling agent and 1.0 kg of titanate coupling agent, and stir to form a uniform solution. When the stirring speed is lower than 25rpm, add 20kg of attapulgite mineral content 98%, specific surface area 168m 2 / g powder, airtight the reactor, energize and heat to 80°C, control the stirring speed to 1500rpm, stir for 1h, and ultrasonically disperse for 20min during this period. After standing to cool, add 1.0kg of polypropylene and 1.0kg of styrene, continue to seal, keep the temperature at 90°C, and stir at 1500rpm for 2h, during which ultrasonic dispersion is 20min. After the solid-liquid separation after cooling, the solid-phase part is dried at 110°C, pulverized by jet mill, and sealed and stored to obtain the attapulgite mineral powder modified by secondary coupling synergistically...
PUM
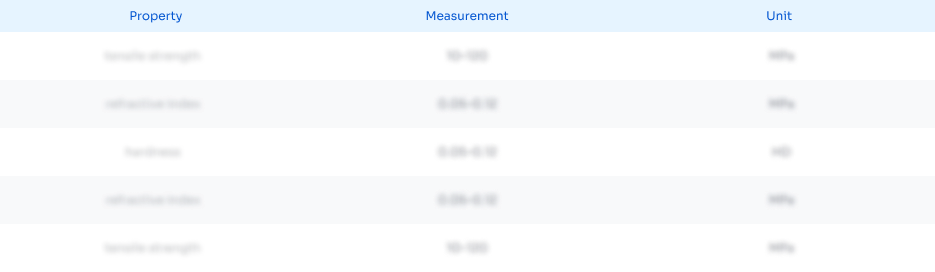
Abstract
Description
Claims
Application Information

- R&D Engineer
- R&D Manager
- IP Professional
- Industry Leading Data Capabilities
- Powerful AI technology
- Patent DNA Extraction
Browse by: Latest US Patents, China's latest patents, Technical Efficacy Thesaurus, Application Domain, Technology Topic, Popular Technical Reports.
© 2024 PatSnap. All rights reserved.Legal|Privacy policy|Modern Slavery Act Transparency Statement|Sitemap|About US| Contact US: help@patsnap.com