Hot working method for improving strength of wrought aluminium alloy and keeping plasticity of wrought aluminium alloy
A technology for deforming aluminum alloys and aluminum alloys, which is applied in the fields of metal and alloy preparation and heat treatment, can solve problems such as industrial production of difficult high-performance aluminum alloys, threats to fatigue life and service safety, and high requirements for equipment performance, achieving long residence time, Save energy and equipment investment, the effect of stable product quality
- Summary
- Abstract
- Description
- Claims
- Application Information
AI Technical Summary
Problems solved by technology
Method used
Image
Examples
Embodiment 1
[0048] AA6061 aluminum alloy ingots were homogenized in a circulating air resistance furnace at 550 °C for 24 hours, then cut and milled, hot-rolled into a 5 mm thick plate, and then solid solution treated and watered at 560 °C for 30 min in an air circulating resistance furnace. Quenching. Then the plate is parked at room temperature (for example, 20°C-25°C) for 30 minutes, and then cold-rolled into a thin plate with a thickness of 1 mm after multiple passes. Then the plate is subjected to aging treatment at 70°C, 120°C, 150°C and 180°C for different times in an oil bath furnace, and the peak aging time of each alloy is found through hardness testing, and the time to reach the peak value is 120h, 12h, 1h and 30min respectively , and then perform tensile tests on the peak-aged aluminum alloy. The artificial aging was carried out in an oil bath furnace with a temperature control accuracy of ±2°C.
Embodiment 2
[0050] AA6061 aluminum alloy ingots were homogenized in a circulating air resistance furnace at 550 °C for 24 hours, then cut and milled, hot-rolled into a 5 mm thick plate, and then solid solution treated and watered at 560 °C for 30 min in an air circulating resistance furnace. Quenching. Then the plate is parked at room temperature (for example, 20°C-25°C) for 1 day, and then cold-rolled into a thin plate with a thickness of 1 mm after multiple passes. Then, the plate is subjected to aging treatment at different times of 70°C, 120°C, 150°C and 180°C in an oil bath furnace, and the peak aging time of each alloy is found through hardness testing. The time to reach the peak value is 120h, 12h, 1h and 10min respectively. ,, and then perform tensile tests on the peak-aged aluminum alloy. The artificial aging was carried out in an oil bath furnace with a temperature control accuracy of ±2°C.
Embodiment 3
[0052] AA6061 aluminum alloy ingots were homogenized in a circulating air resistance furnace at 550 °C for 24 hours, then cut and milled, hot-rolled into a 5 mm thick plate, and then solid solution treated and watered at 560 °C for 30 min in an air circulating resistance furnace. Quenching. Then the plate is parked at room temperature (for example, 20°C-25°C) for 2 weeks, and finally cold-rolled into a 1mm thick sheet through multiple passes. Then, the plate is subjected to aging treatment at 70°C, 120°C, 150°C and 180°C for different times in an oil bath furnace, and the peak aging time of each alloy is found through hardness testing, and the time to reach the peak value is 120h, 10h, 1h and 10min respectively Then, the tensile test was carried out on the aluminum alloy in the peak aging state, and the aging treatment time at 120°C was 8h, and that at 150°C was 1h. The artificial aging was carried out in an oil bath furnace with a temperature control accuracy of ±2°C.
PUM
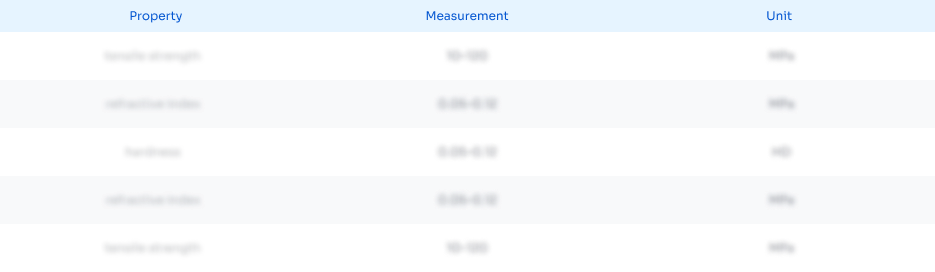
Abstract
Description
Claims
Application Information

- Generate Ideas
- Intellectual Property
- Life Sciences
- Materials
- Tech Scout
- Unparalleled Data Quality
- Higher Quality Content
- 60% Fewer Hallucinations
Browse by: Latest US Patents, China's latest patents, Technical Efficacy Thesaurus, Application Domain, Technology Topic, Popular Technical Reports.
© 2025 PatSnap. All rights reserved.Legal|Privacy policy|Modern Slavery Act Transparency Statement|Sitemap|About US| Contact US: help@patsnap.com