Safe production method of nitro-compound
A technology for nitrobenzene and nitration reaction, which is applied in the preparation of nitro compounds, organic chemistry, nitrate preparation, etc., can solve the problems of unevenness, increased side reactions, low product quality, etc., and achieves full and uniform contact and dangerous degree. The effect of reducing and avoiding side effects
- Summary
- Abstract
- Description
- Claims
- Application Information
AI Technical Summary
Problems solved by technology
Method used
Image
Examples
Embodiment 1
[0033] Embodiment 1 prepares the method for nitrobenzene
[0034] Specific steps include:
[0035] 1) Using the HL-50 centrifugal extractor developed by Beijing Institute of Extraction Applied Technology as the nitration reaction separator, connect four separators in series according to the method described in the above-mentioned specific embodiment, so that water: nitric acid: sulfuric acid = 7:45 : The mixed acid solution prepared in the weight ratio of 48 is fed from the heavy phase inlet of the first nitration reaction separator, and benzene is fed from the light phase inlet of the fourth nitration reaction separator, and the mixed acid solution and benzene are continuously sent simultaneously by the metering pump. into the nitration reaction separator, wherein the feed molar ratio of benzene and nitric acid is 1:1.02, and the mixed acid and benzene carry out nitration reaction at a temperature of 60-80°C and a speed of 1100-1300 rpm; 2) each nitration In the reaction sep...
Embodiment 2
[0038] Embodiment 2 prepares the method for nitrobenzene
[0039] The process is the same as in Example 1, changing the mixed acid to form water: nitric acid: sulfuric acid=30:4:66, the feed molar ratio of benzene and nitric acid is 1.1:1.0, the temperature of mixed acid and benzene at 136°C and 900 rpm The nitrification reaction is carried out under the rotating speed;
[0040] The purity of the nitrobenzene product obtained in this embodiment is 99.5%, and the yield is 99.1%.
Embodiment 3
[0041] Embodiment 3 prepares the method for o-nitrotoluene
[0042] The process is the same as in Example 1, the mixed acid ratio is changed to water: nitric acid: sulfuric acid=20:56:24, the feed molar ratio of benzene to nitric acid is 1.0:1.05, the mixed acid and toluene are mixed at a temperature of 50°C and 1000 rpm The nitration reaction is carried out at a high speed; after the reaction is completed, the crude nitrates are rectified to obtain o-nitrotoluene, p-nitrotoluene and m-nitrotoluene.
[0043] The purity of the nitrotoluene product obtained in this embodiment is 98%, and the total yield is 94.5%.
PUM
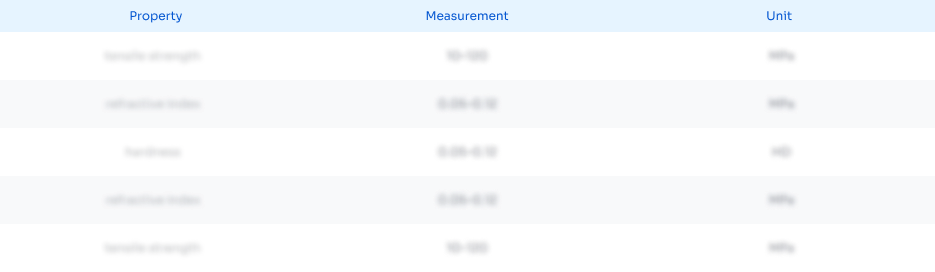
Abstract
Description
Claims
Application Information

- R&D
- Intellectual Property
- Life Sciences
- Materials
- Tech Scout
- Unparalleled Data Quality
- Higher Quality Content
- 60% Fewer Hallucinations
Browse by: Latest US Patents, China's latest patents, Technical Efficacy Thesaurus, Application Domain, Technology Topic, Popular Technical Reports.
© 2025 PatSnap. All rights reserved.Legal|Privacy policy|Modern Slavery Act Transparency Statement|Sitemap|About US| Contact US: help@patsnap.com