Marine anticorrosive powdered paint and preparation method thereof
A powder coating and marine anti-corrosion technology, applied in anti-corrosion coatings, powder coatings, coatings, etc., can solve the problems of PE water permeability, high air permeability, poor anti-corrosion effect, and inability to do it, and achieve the effect of improving the anti-corrosion effect.
- Summary
- Abstract
- Description
- Claims
- Application Information
AI Technical Summary
Problems solved by technology
Method used
Examples
Embodiment 1
[0040] Marine anti-corrosion powder coating 1, the formulation of the coating includes medium density polyethylene (MDPE), glass flakes and spherical zinc powder. Among them, 100 kg of MDPE, 5 kg of glass flakes, and 30 kg of spherical zinc powder.
[0041] Preparation of the above raw materials:
[0042] Mix the above-mentioned medium density polyethylene (MDPE), glass flakes and spherical zinc powder in a mixer evenly for 5 minutes, and then put them in a screw extruder for granulation at a temperature of 190-230°C and a speed of 300-500r / min to get plastic particles, and then grind these particles in a mill to get that.
Embodiment 2
[0044] Marine anti-corrosion powder coating 2, the formulation of the coating includes high-density polyethylene (HDPE), flake glass, flake zinc powder and lubricant. Among them, 100 kg of HDPE, 20 kg of flake neutral glass, 5 kg of flake zinc powder, and 0.1 kg of lubricant.
[0045] Preparation of the above raw materials:
[0046] Mix the HDPE, flake glass, flake zinc powder and lubricant in the above formula evenly in a mixer for 10 minutes, and then put it into a screw extruder to granulate at a temperature of 190-230°C and a speed of 300-500r / min to obtain plastic particles, and then grind these particles in a mill to obtain the final product.
Embodiment 3
[0048]Marine anti-corrosion powder coating 3, the formulation of the coating includes low-density polyethylene (LDPE), high-density polyethylene (HDPE), flake glass, flake zinc powder and lubricants. Among them, 50 kg of LDPE, 50 kg of HDPE, 30 kg of flake neutral glass, 20 kg of flake zinc powder, and 1 kg of lubricant.
[0049] Preparation of the above raw materials:
[0050] Mix LDPE, HDPE, flaky neutral glass, flaky zinc powder and lubricant in a mixer for 10 minutes, and then put them in a screw extruder for granulation at a temperature of 190-230°C and a speed of 300-500r / min, to obtain plastic particles, and then grind these particles in a mill, that is.
PUM
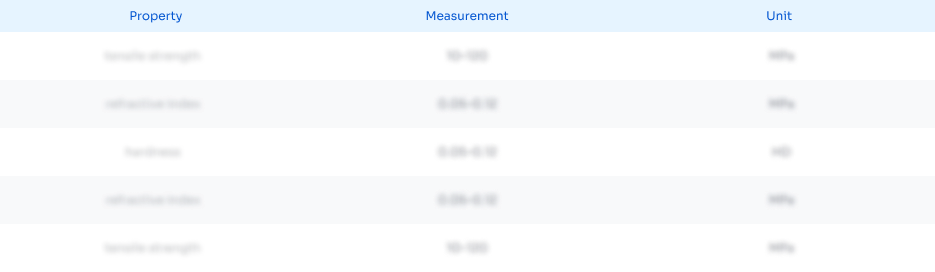
Abstract
Description
Claims
Application Information

- R&D
- Intellectual Property
- Life Sciences
- Materials
- Tech Scout
- Unparalleled Data Quality
- Higher Quality Content
- 60% Fewer Hallucinations
Browse by: Latest US Patents, China's latest patents, Technical Efficacy Thesaurus, Application Domain, Technology Topic, Popular Technical Reports.
© 2025 PatSnap. All rights reserved.Legal|Privacy policy|Modern Slavery Act Transparency Statement|Sitemap|About US| Contact US: help@patsnap.com