Halogen-free flame retardant and preparation method thereof
A technology of flame retardant and hypophosphite, which is applied in the field of halogen-free flame retardants and its preparation, can solve the problems of high addition of halogen-free flame retardants, waste of raw materials, spontaneous combustion of red phosphorus, etc., and achieves obvious effects and flame retardant The effect is good and the steps are simple
- Summary
- Abstract
- Description
- Claims
- Application Information
AI Technical Summary
Problems solved by technology
Method used
Image
Examples
Embodiment 1
[0035] Put TGIC (triglycidyl isocyanurate) and magnesium hypophosphite with an equivalent ratio of 1:1 into the reaction vessel, use ethanol as the solvent, slowly heat to 70℃, heat and stir to reflux for 10 hours, cool and filter, wash with water, and dry to obtain the target Compound I.
Embodiment 2
[0037] Put TGIC (triglycidyl isocyanurate) and sodium hypophosphite with an equivalent ratio of 1:2 into the reaction vessel, use ethylene glycol as the solvent, slowly heat to 150°C, stir and reflux for 4 hours, cool, filter, and wash with water. After drying, the target compound II is obtained.
Embodiment 3
[0039] Put TGIC (triglycidyl isocyanurate) and potassium hypophosphite with an equivalent ratio of 1:3.5 into the reaction vessel, use ethanol as the solvent, slowly heat to 100°C, heat and stir to reflux for 6 hours, cool and filter, wash with water, and dry to obtain the target Compound III.
PUM
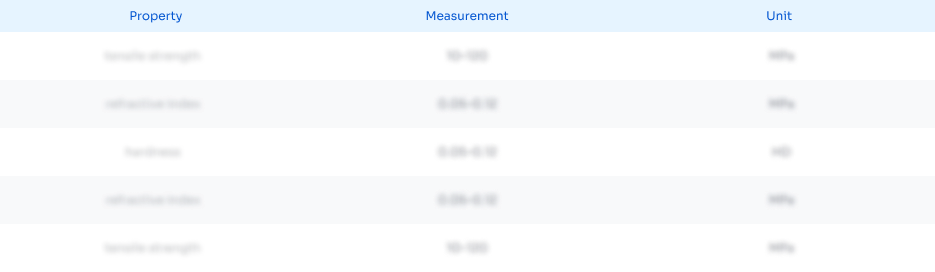
Abstract
Description
Claims
Application Information

- R&D Engineer
- R&D Manager
- IP Professional
- Industry Leading Data Capabilities
- Powerful AI technology
- Patent DNA Extraction
Browse by: Latest US Patents, China's latest patents, Technical Efficacy Thesaurus, Application Domain, Technology Topic, Popular Technical Reports.
© 2024 PatSnap. All rights reserved.Legal|Privacy policy|Modern Slavery Act Transparency Statement|Sitemap|About US| Contact US: help@patsnap.com