Method for producing 4-hexene-3-ketone by carrying out catalytic dehydration on 4-hydroxy-3-hexanone
A technology of catalytic dehydration and hexanone, applied in chemical instruments and methods, preparation of carbon-based compounds, preparation of organic compounds, etc., can solve the problems of high reaction temperature, low space velocity, poor catalyst activity, etc., and achieve good technical effects. Effect
- Summary
- Abstract
- Description
- Claims
- Application Information
AI Technical Summary
Problems solved by technology
Method used
Image
Examples
Embodiment 1
[0019] Dissolve 30 grams of aluminum nitrate in 25 grams of deionized water, take 20 grams of silica gel carrier, impregnate the above solution at 20 ° C, take it out after 3 hours and dry it at 120 ° C for 5 hours, put it in a muffle furnace and bake it at 600 ° C for 4 hours, after cooling The catalyst A is obtained by taking out and impregnating for the second time, drying and roasting. Al in the catalyst 2 o 3 The parts by weight of the surface coating is 23 parts, SiO 2 The parts by weight of the inner core are 77 parts. The performance evaluation of the catalyst was carried out on a fixed-bed reaction device at normal pressure. A stainless steel reactor with an inner diameter of 10 mm was used. The loading amount of the catalyst was 10 ml, the reaction temperature was 350 °C, and the liquid space velocity was 1 hour. -1 , reacted under normal pressure. The reaction product was analyzed by HP 6890 gas chromatography, hydrogen flame detector, and HP-6 capillary column ...
Embodiment 2
[0021] Dissolve 20 grams of aluminum sulfate in 100 grams of deionized water, take 20 grams of silica carrier, impregnate the above solution at 50°C, take it out after 4 hours, dry it at 100°C for 6 hours, and bake it in a muffle furnace at 500°C for 5 hours. After cooling, the catalyst B is obtained by taking it out, impregnating it twice, drying it, and roasting it. Al in the catalyst 2 o 3 The parts by weight of the surface coating is 25 parts, SiO 2 The parts by weight of the inner core are 75 parts. Catalyst performance was evaluated according to the conditions of [Example 1], except that the reaction temperature was 260°C and the liquid space velocity was 3 hours -1 . The reaction results are shown in Table 1.
Embodiment 3
[0023] Dissolve 12 grams of aluminum nitrate in 20 grams of deionized water, take 15 grams of white carbon black carrier, impregnate the above solution at 70 ° C, take it out after 2 hours and dry it at 110 ° C for 4 hours, put it in a muffle furnace and bake it at 650 ° C for 4 hours, Catalyst C is obtained. Al in the catalyst 2 o 3 The parts by weight of the surface coating is 14 parts, SiO 2 The parts by weight of the kernel are 86 parts. Evaluation catalyst performance by the condition of [embodiment 1], just reaction temperature is 270 ℃, and liquid space velocity is 8 hours -1 . The reaction results are shown in Table 1.
PUM
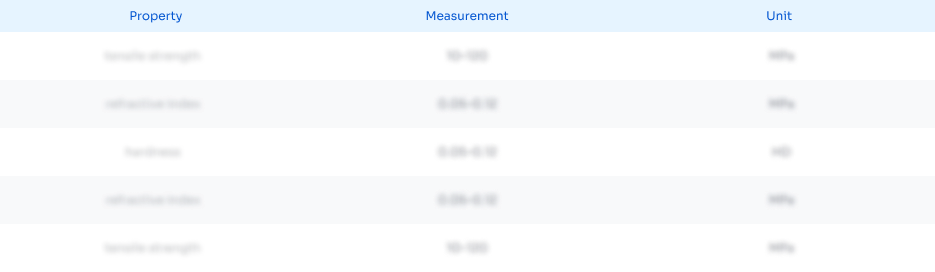
Abstract
Description
Claims
Application Information

- R&D
- Intellectual Property
- Life Sciences
- Materials
- Tech Scout
- Unparalleled Data Quality
- Higher Quality Content
- 60% Fewer Hallucinations
Browse by: Latest US Patents, China's latest patents, Technical Efficacy Thesaurus, Application Domain, Technology Topic, Popular Technical Reports.
© 2025 PatSnap. All rights reserved.Legal|Privacy policy|Modern Slavery Act Transparency Statement|Sitemap|About US| Contact US: help@patsnap.com