Catalytic cracking material for reducing sulfur content of gasoline and preparation method thereof
A technology of catalytic cracking and sulfur content, which is applied in the direction of catalytic cracking, chemical instruments and methods, cracking, etc., can solve the problems of reducing the sulfur content of gasoline in the catalytic cracking process, low addition amount, etc., and achieves convenient application, low roasting temperature, The effect of simple preparation method
- Summary
- Abstract
- Description
- Claims
- Application Information
AI Technical Summary
Problems solved by technology
Method used
Image
Examples
Embodiment 1
[0028] In this embodiment, the vanadium-containing mullite material is prepared. Take 8g of ammonium metavanadate, add 2000mL of deionized water, add oxalic acid until the solid is completely dissolved, then add 600g of Suzhou kaolin, soak at 85°C for 6 hours, dry at 120°C, grind through a 100-mesh sieve, and roast at 1250°C for 1 hour to prepare the vanadium-containing Mullite material. The vanadium-containing mullite material was washed three times with dilute oxalic acid solution, washed with deionized water until neutral, and dried at 120°C. The obtained sample number is V1. X-ray fluorescence spectrometry analysis of the vanadium content in the sample, and converted to V 2 o 5 Measurement, the vanadium content of the sample is 1.5%; XRD analysis of the sample crystal phase, the XRD spectrum of V1 is shown in the attached figure, the characteristic peak of mullite is marked with black dots in the figure; the mullite content is 85% according to the measurement and calcul...
Embodiment 2
[0030] In this embodiment, the vanadium-containing mullite material is prepared. Take 35g of ammonium metavanadate, add 2000mL of deionized water, add oxalic acid until the solid is completely dissolved, then add 600g of Suzhou kaolin spray microspheres (from Shanghai Naco Auxiliary Co., Ltd.), soak at 85°C for 6 hours, and dry at 120°C. Grinding through a 100-mesh sieve, calcining at 950° C. for 3 hours to prepare the vanadium-containing mullite material. The vanadium-containing mullite material was washed three times with dilute oxalic acid solution, washed with deionized water until neutral, and dried at 120°C. The obtained sample number is V2. X-ray fluorescence spectrometry analyzes the vanadium content in the sample and converts it to V 2 o 5 Measurement, the vanadium content of the sample was 7.2%; XRD analysis of the crystal phase of the sample determined that the mullite content was 68%.
Embodiment 3
[0032]In this embodiment, the vanadium-containing mullite material is prepared. Take 110g of vanadyl sulfate, add 300mL of deionized water until the solid is completely dissolved, then add 600g of Suzhou kaolin, stir and mix thoroughly for 6 hours at 85°C, filter, dry the filter cake at 120°C, grind through a 100-mesh sieve, and roast at 900°C for 5h The vanadium-containing mullite material is prepared. The vanadium-containing mullite material was washed three times with dilute oxalic acid solution, washed with deionized water until neutral, and dried at 120°C. The obtained sample number is V3. X-ray fluorescence spectrometry analysis of the vanadium content in the sample, and converted to V 2 o 5 Measurement, the vanadium content of the sample is 17%; XRD analysis of the crystal phase of the sample shows that the mullite content is 66%.
PUM
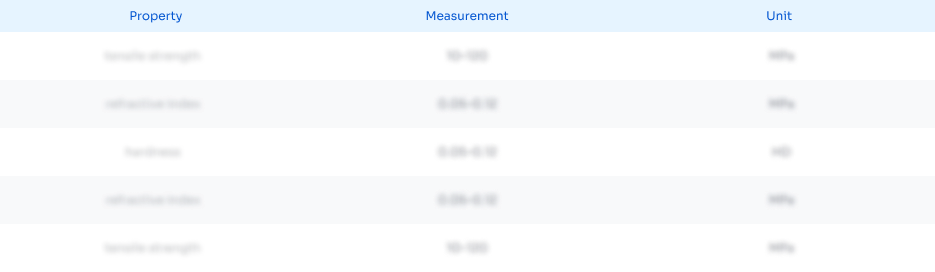
Abstract
Description
Claims
Application Information

- R&D
- Intellectual Property
- Life Sciences
- Materials
- Tech Scout
- Unparalleled Data Quality
- Higher Quality Content
- 60% Fewer Hallucinations
Browse by: Latest US Patents, China's latest patents, Technical Efficacy Thesaurus, Application Domain, Technology Topic, Popular Technical Reports.
© 2025 PatSnap. All rights reserved.Legal|Privacy policy|Modern Slavery Act Transparency Statement|Sitemap|About US| Contact US: help@patsnap.com