Plate-fin type heat exchanger with fluid being flowing back and forth in channel
A plate-fin heat exchanger and internal fluid technology, which is applied to the types of heat exchangers, heat exchanger shells, indirect heat exchangers, etc., can solve the problems of low average heat exchange efficiency, increased production costs, and complicated manufacturing processes, etc. problem, to achieve the effect of small space occupation, reduced production cost and simple production process
- Summary
- Abstract
- Description
- Claims
- Application Information
AI Technical Summary
Problems solved by technology
Method used
Image
Examples
Embodiment 1
[0040] This embodiment provides a plate-fin heat exchanger, which can be used in a cryogenic multi-component mixed working fluid throttling refrigeration system to realize refrigeration in a 100K temperature zone. See figure 1 , 2 , 3, 4, 5, 6, 9 and Figure 10 , a plate-fin heat exchanger in which the fluid in the channel turns back and flows, which includes:
[0041] A heat exchanger shell 1 composed of left and right vertical shell plates; a vertical channel partition 2 placed between the left and right vertical shell plates at intervals; the left and right vertical shell plates are adjacent to it Horizontal edge seals and left and right vertical edge seals are respectively provided at the peripheral edges between the vertical channel partitions 2 of adjacent channels and the peripheral edges between the vertical channel partitions 2 of adjacent channels to form heat exchange channels; The heat exchange channels are divided into hot channels and cold channels distributed...
Embodiment 2
[0053] Embodiment 2: A plate-fin heat exchanger related to the present invention is used in a large-scale natural gas liquefaction refrigeration system to realize natural gas liquefaction.
[0054] It is basically the same as that of Example 1, the difference is that in each cold channel in the heat exchanger, 6 horizontally placed cold runner horizontal adjustment slats are set to divide the channel into 7 horizontal runners and 6 vertical runners. In each hot channel of the heat exchanger, 5 horizontally placed hot runner horizontal adjustment strips are set to divide the channel into a return channel composed of 6 horizontal channels and 5 vertical channels. Shaped runner. Among the 7 horizontal flow channels in the cold aisle, except for the bottom 3, the other 4 horizontal flow channels are all equipped with horizontal serrated fins with the same wing pitch, and the bottom 3 flow channels are each equipped with The fin group composed of 4 kinds of fins with different pit...
Embodiment 3
[0056] Embodiment 3: A plate-fin heat exchanger related to the present invention is used in a large-scale natural gas liquefaction refrigeration system to realize natural gas liquefaction.
[0057] It is basically the same as Embodiment 1, the difference is: a square dispersion fin is set in the vertical flow channel of the cold aisle and the hot aisle, such as Figure 7 , which is conducive to the uniform distribution of fluid in the flow channel.
PUM
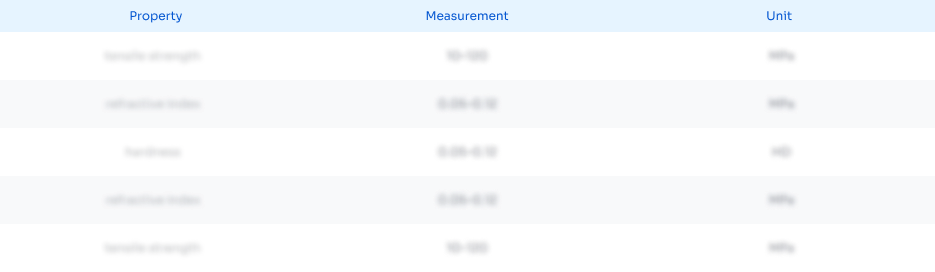
Abstract
Description
Claims
Application Information

- R&D
- Intellectual Property
- Life Sciences
- Materials
- Tech Scout
- Unparalleled Data Quality
- Higher Quality Content
- 60% Fewer Hallucinations
Browse by: Latest US Patents, China's latest patents, Technical Efficacy Thesaurus, Application Domain, Technology Topic, Popular Technical Reports.
© 2025 PatSnap. All rights reserved.Legal|Privacy policy|Modern Slavery Act Transparency Statement|Sitemap|About US| Contact US: help@patsnap.com