Process for producing bamboo charcoal polypropylene composite fibers
A composite fiber and production process technology, applied in the field of textile fabrics, can solve the problems of large difference between dry and wet strength, difficult to solve the dispersion uniformity, low strength of viscose fiber, etc. Good sun resistance
- Summary
- Abstract
- Description
- Claims
- Application Information
AI Technical Summary
Problems solved by technology
Method used
Examples
Embodiment 1
[0014] (1) Mix 10g of bamboo charcoal micropowder with 110g of polypropylene slices, so that the bamboo charcoal micropowder is uniformly dispersed in the polypropylene slices, and extruded by a twin-screw extruder to obtain bamboo charcoal masterbatch;
[0015] (2) Mix 10g of bamboo charcoal masterbatch with 120g of polypropylene slices, heat and dry at 140°C under nitrogen protection, spin through a melt spinning machine, oil, and wind to form bamboo charcoal polypropylene composite fibers.
Embodiment 2
[0017] (1) Mix 10g of bamboo charcoal micropowder with 130g of polypropylene slices, so that the bamboo charcoal micropowder is uniformly dispersed in the polypropylene slices, and extruded by a twin-screw extruder to obtain bamboo charcoal masterbatch;
[0018] (2) Mix 10g of bamboo charcoal masterbatch with 140g of polypropylene slices, heat and dry at 160°C under the protection of nitrogen and argon mixed gas, spin through a melt spinning machine, oil, and wind to form bamboo charcoal polypropylene composite fibers .
Embodiment 3
[0020] (1) 10g of bamboo charcoal micropowder is mixed with 150g of polypropylene slices, so that the bamboo charcoal micropowder is evenly dispersed in the polypropylene slices, and extruded by a twin-screw extruder to obtain bamboo charcoal masterbatch;
[0021] (2) Mix 10g of bamboo charcoal masterbatch with 120g of polypropylene slices, heat and dry at 150°C under the protection of argon, spin through a melt spinning machine, oil, and wind to form bamboo charcoal polypropylene composite fibers.
[0022] The production process of the bamboo charcoal polypropylene composite fiber disclosed by the present invention has high elongation rate of the prepared fiber, small difference between dry and wet strength, high strength, good shape stability, can improve the durability of the fabric, and the fabric has good sunlight resistance and is fluffy The bamboo charcoal added at the same time also has functional properties such as adsorption and antibacterial, is simple to prepare, re...
PUM
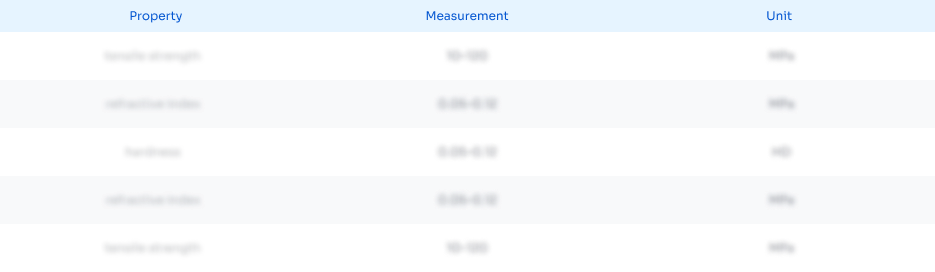
Abstract
Description
Claims
Application Information

- R&D Engineer
- R&D Manager
- IP Professional
- Industry Leading Data Capabilities
- Powerful AI technology
- Patent DNA Extraction
Browse by: Latest US Patents, China's latest patents, Technical Efficacy Thesaurus, Application Domain, Technology Topic, Popular Technical Reports.
© 2024 PatSnap. All rights reserved.Legal|Privacy policy|Modern Slavery Act Transparency Statement|Sitemap|About US| Contact US: help@patsnap.com