Raw material pretreatment process for extracting vanadium from vanadium slag
A technology for pretreatment and vanadium slag, applied in the field of vanadium extraction from vanadium slag, can solve problems such as pollution, waste of raw materials, unfavorable costs, etc., and achieve the effects of reducing production costs, increasing conversion rate, and reducing vanadium loss
- Summary
- Abstract
- Description
- Claims
- Application Information
AI Technical Summary
Problems solved by technology
Method used
Image
Examples
Embodiment 1
[0032] Embodiment one inventive method handles vanadium slag
[0033] The vanadium slag is in the form of black fine particles, and the mass fraction of the main components is shown in Table 1:
[0034] Table 1 Main components of vanadium slag
[0035] name
V 2 o 5 / %
-120mesh / %
MFe / %
h 2 O / %
Vanadium-containing residue
1.60
45.0
2.5
20.0
[0036] Add quantitative water to the vanadium slag with the particle size in Table 1, put it into a wet ball mill (model ∮1.5×5.7m) according to the volume of vanadium slag: water = 1:3, and grind it finely. 2mm)" to screen out large particles of metallic iron and control it within the qualified range, that is, MFe≤1.0%. The particle size of vanadium slag after ball milling is controlled at -120 mesh and the amount is ≥85.0%. The slurry passes through a rubber belt filter ( The model is DU25 / 1800) and the suction filter is clean, and the moisture content of the wet abrasive is c...
Embodiment 2
[0044] Embodiment two inventive method handles vanadium slag
[0045] The vanadium slag is in the form of black fine particles, and the mass fraction of the main components is shown in Table 1.
[0046] Add quantitative water to the vanadium slag with the particle size in Table 1, put it into a wet ball mill (model ∮1.5×5.7m) according to the volume of vanadium slag: water = 1:3, and grind it finely. 2mm)" to screen out large particles of metallic iron and control it within the qualified range, that is, MFe≤1.0%. The particle size of vanadium slag after ball milling is controlled at -120 mesh and the amount is ≥85.0%. The slurry passes through a rubber belt filter ( The model is DU25 / 1800), and the water content of the wet abrasive is controlled between 15 and 20%, which meets the process requirements. The throughput is 230 tons / 24 hours, which fully meets the production requirements of 2 lines. The specific process indicators of the wet abrasive are shown in the table 4.
...
PUM
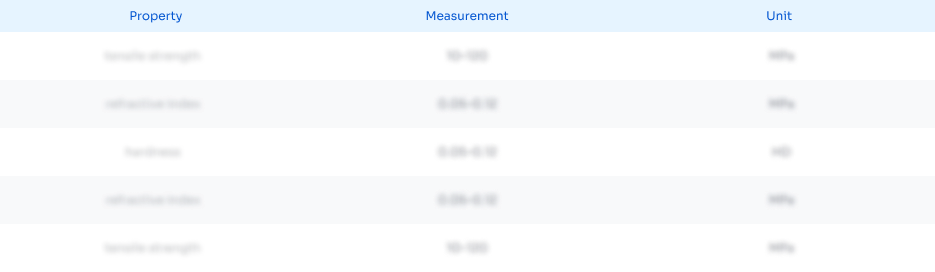
Abstract
Description
Claims
Application Information

- R&D
- Intellectual Property
- Life Sciences
- Materials
- Tech Scout
- Unparalleled Data Quality
- Higher Quality Content
- 60% Fewer Hallucinations
Browse by: Latest US Patents, China's latest patents, Technical Efficacy Thesaurus, Application Domain, Technology Topic, Popular Technical Reports.
© 2025 PatSnap. All rights reserved.Legal|Privacy policy|Modern Slavery Act Transparency Statement|Sitemap|About US| Contact US: help@patsnap.com