Bisphthalonitrile-amino phenoxy phthalonitrile copolymer and condensate, and glass fiber composite material and preparation method thereof
An aminophenoxy phthalonitrile and diphthalonitrile technology, applied in the field of polymer materials, can solve the problems of slow curing reaction, troublesome synthesis steps, non-curing, etc., achieve excellent flame retardant performance, easy to use Achieving, easy-to-control effects
- Summary
- Abstract
- Description
- Claims
- Application Information
AI Technical Summary
Problems solved by technology
Method used
Image
Examples
Embodiment 1-5
[0035] Embodiment 1-5 Bisphenol A type bisphthalonitrile-aminophenoxyphthalonitrile copolymer and its preparation
[0036] Put bisphenol A type bisphthalonitrile in a beaker, stir and melt at 200°C-220°C, continue to stir for 5-10min, then slowly add 3-aminophenoxyphthalonitrile, then stir for 10 minutes -30min, a dark green molten liquid was obtained. After it was cooled to room temperature, it was ground into powder to obtain the powder of bisphenol A type bisphthalonitrile / 3-aminophenoxyphthalonitrile copolymer. The various performances of gained different proportioning 3-aminophenoxyphthalonitrile / bisphenol A type bisphthalonitrile copolymer powder are as shown in table 1:
[0037] Table 1 Properties of bisphenol A type bisphthalonitrile / 3-aminophenoxyphthalonitrile copolymer
[0038]
Embodiment 6-10
[0039] Example 6-10 Bisphenol A type bisphthalonitrile / 3-aminophenoxyphthalonitrile cured product and its preparation
[0040] Take the bisphenol A type bisphthalonitrile / 3-aminophenoxyphthalonitrile copolymer powder obtained in Examples 1-5, stir and fully melt at 150-200 ° C, and pour it after 5-10 minutes. Heat treatment molding to obtain bisphenol A type bisphthalonitrile / 3-aminophenoxyphthalonitrile cured product; wherein, the heat treatment temperature is 200°C / 2h, 240°C / 2h, 280°C / 4h, 320°C / 4h; the flame retardancy and heat resistance of the obtained cured product are shown in Table 2:
[0041] Table 2 Properties of bisphenol A bisphthalonitrile / 3-aminophenoxyphthalonitrile cured product
[0042]
Embodiment 11-17
[0043] Example 11-17 Bisphenol A type bisphthalonitrile / 3-aminophenoxyphthalonitrile glass fiber composite material and its preparation
[0044] In order to prepare bisphenol A bisphthalonitrile / 3-aminophenoxyphthalonitrile glass fiber composites with excellent comprehensive properties, we use three processes: (1) dry method; (2) wet method (3) dry-wet mixing method, the copolymer obtained in Example 3 was selected to add glass fiber to prepare a composite sheet (the weight ratio of bisphenol A type diphthalonitrile and 3-aminophenoxyphthalonitrile The ratio is 50:50), of which, the mass of glass fiber accounts for 62.5 parts, and the mass of bisphenol A type bisphthalonitrile / 3-aminophenoxyphthalonitrile copolymer powder accounts for 37.5 parts. The three processes The weight ratio of bisphenol A type diphthalonitrile and 3-aminophenoxyphthalonitrile is 50:50; specifically as follows:
PUM
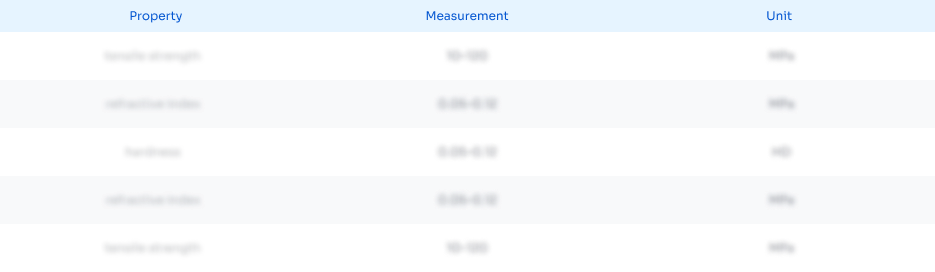
Abstract
Description
Claims
Application Information

- R&D
- Intellectual Property
- Life Sciences
- Materials
- Tech Scout
- Unparalleled Data Quality
- Higher Quality Content
- 60% Fewer Hallucinations
Browse by: Latest US Patents, China's latest patents, Technical Efficacy Thesaurus, Application Domain, Technology Topic, Popular Technical Reports.
© 2025 PatSnap. All rights reserved.Legal|Privacy policy|Modern Slavery Act Transparency Statement|Sitemap|About US| Contact US: help@patsnap.com