Multi-element combined-type low-pressure pouring method and combined-type sand core
A pouring method and combined technology, applied in the direction of core, casting molding equipment, casting molds, etc., can solve the problems of not being able to meet the requirements of casting forming and quality, and improve the compactness, improve the filling ability, The effect of improving the pass rate
- Summary
- Abstract
- Description
- Claims
- Application Information
AI Technical Summary
Problems solved by technology
Method used
Image
Examples
Embodiment Construction
[0030] The method of the present invention will be described in detail below in conjunction with the accompanying drawings.
[0031] In this embodiment, the casting to be cast is a casting with an inner and outer two-layer skin structure, and the multi-component combined low-pressure pouring method includes the following steps:
[0032] A. Prepare a combined sand core composed of multiple sub-sand cores according to the structural shape of the casting;
[0033] Since the casting to be cast has an inner and outer skin structure, the main sand core can be divided into an inner sand core 1 and an outer sand core 2 according to this structure;
[0034] The gate sand core 3 is prepared, and the gate sand core 3 is provided with a main gate 31 , a runner 32 communicating with the main gate 31 , a rain runner 33 and a gap runner 34 communicating with the runner 32 .
[0035] The sprue sand core 3 is combined with the inner layer sand core 1 and the outer layer sand core 2 as a whole...
PUM
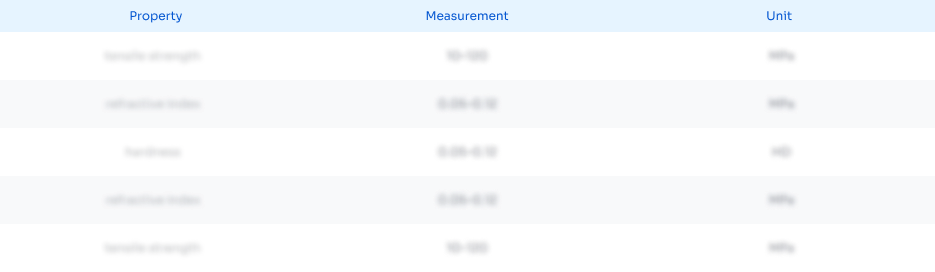
Abstract
Description
Claims
Application Information

- R&D
- Intellectual Property
- Life Sciences
- Materials
- Tech Scout
- Unparalleled Data Quality
- Higher Quality Content
- 60% Fewer Hallucinations
Browse by: Latest US Patents, China's latest patents, Technical Efficacy Thesaurus, Application Domain, Technology Topic, Popular Technical Reports.
© 2025 PatSnap. All rights reserved.Legal|Privacy policy|Modern Slavery Act Transparency Statement|Sitemap|About US| Contact US: help@patsnap.com