One-bath dyeing of pure cotton knitted fabrics by deoxidizing and polishing
A technology of knitted fabric and bath method is applied in the field of deoxidizing, polishing, and one-bath dyeing of pure cotton knitted fabrics, which can solve the problems of insufficient polishing effect, complicated and strict operation, and lengthy process.
- Summary
- Abstract
- Description
- Claims
- Application Information
AI Technical Summary
Problems solved by technology
Method used
Examples
Embodiment 1
[0019] In this embodiment, the sample to be treated is pure cotton knitted fabric. Dye the sample to be treated according to the following process: after boiling and rinsing, drain the liquid—wash in hot water (cooling water) for 10 minutes—put in soft water and raise the temperature to 60°C—add HAC (acetic acid) and run for 10 minutes, and adjust the pH value to 6 -7—Add polishing enzyme 988—Run for 15 minutes—Add dye (30 minutes)—Run for 15 minutes—Add Yuanming powder in batches (30 minutes in total)—Run for 30 minutes—Add soda ash in batches (40 minutes in total)—Insulation 60 minutes—after treatment (washing, pickling, soaping, washing, washing)—cloth output—softening agent (special softening machine).
[0020] Among them, polishing enzyme 988 is cellulosic enzyme, the addition amount is 1.5% (mass percentage), and the dyeing bath ratio is 1:10; Yuanming powder is added in 2 times, the first time adding 1 / 3 of the total mass, the second time The addition amount is 2 / 3 of ...
Embodiment 2
[0022] The settings and process flow of this example are the same as those of Example 1, the difference is that the addition of polishing enzyme 988 is 1% (mass percentage), and the dyeing bath ratio is 1:5.
Embodiment 3
[0024] The settings and process flow of this example are the same as those of Example 1, except that the addition of polishing enzyme 988 is 2% (mass percentage), and the dyeing bath ratio is 1:20.
[0025] The technical index characterization of above-mentioned embodiment:
[0026] a. After the technical solution of this embodiment is used, the color fastness index of the fabric is as follows: the soaping level is 4 grades, the dry rubbing fastness is 4 grades, and the wet rubbing fastness is 3 grades, and the cloth surface is smooth and colorless.
[0027] b. In terms of comprehensive production cost:
[0028] 1. In the technical scheme of this embodiment, only one auxiliary agent of 988 polishing enzyme is added in the process flow. When the dosage is calculated at 1.5%, the auxiliary agent cost: 15KG / ton of cloth×38 yuan / KG=570 yuan / ton of cloth; In the prior art, after the cloth is boiled, 0.15% TY is used to remove oxygen, and then 0.65% CTA-CL3 and 0.5% HAC are used to...
PUM
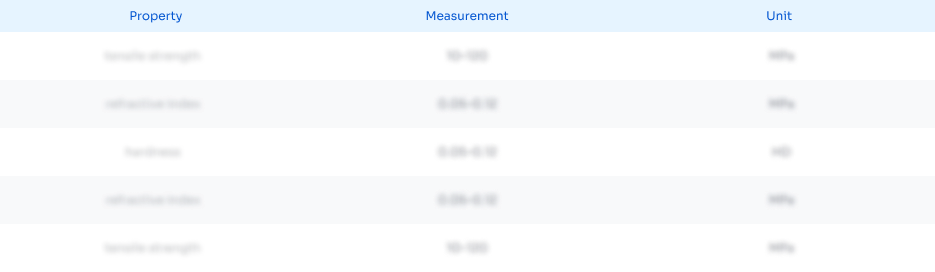
Abstract
Description
Claims
Application Information

- R&D
- Intellectual Property
- Life Sciences
- Materials
- Tech Scout
- Unparalleled Data Quality
- Higher Quality Content
- 60% Fewer Hallucinations
Browse by: Latest US Patents, China's latest patents, Technical Efficacy Thesaurus, Application Domain, Technology Topic, Popular Technical Reports.
© 2025 PatSnap. All rights reserved.Legal|Privacy policy|Modern Slavery Act Transparency Statement|Sitemap|About US| Contact US: help@patsnap.com