Method for preparing direct-reduction iron by reducing carbon-containing iron ore powder in microwave heating manner
A technology for microwave heating and iron reduction, applied in furnaces, furnace types, fluidized bed furnaces, etc., can solve the problems of uneven temperature distribution of materials, difficult product quality control, large floor space, etc., to achieve environmentally friendly production, reduce Human workload, the effect of reducing emissions
- Summary
- Abstract
- Description
- Claims
- Application Information
AI Technical Summary
Problems solved by technology
Method used
Image
Examples
Embodiment 1
[0026] A. Mix oxidized slag and iron concentrate at a mass percentage of 40:60, mix coke powder and anthracite powder at a mass percentage of 50:50 as a reducing agent, and use 70% iron raw material, 25% reducing agent, The proportion of lightly burned dolomite 5% is blended evenly.
[0027] B. Spread the raw materials prepared in the above step A in a loose shape on the material tray, the height of the material layer is 40mm, push the material tray into the microwave pusher kiln, heat up to 1100°C, reduce for 160min, pump air for 10s every 15min, and then cool it out Iron and iron slag are separated to obtain direct reduced iron products with TFe87.43%, MFe76.07%, and metallization rate of 87.21%.
Embodiment 2
[0029] A. Mix the oxidized slag and iron concentrate at a mass percentage of 35:65, and mix them evenly in proportions of 63% iron raw material, 30% high-quality anthracite powder, and 7% limestone;
[0030] B. Spread the raw materials prepared in the above step A in a loose shape on the material tray, the height of the material layer is 45mm, after the material tray is pushed into the microwave pusher kiln, the temperature is raised to 1150°C, reduced for 180min, ventilated for 10s every 15min, and then cooled out Iron and iron slag are separated to obtain direct reduced iron products with TFe82.43%, MFe74.08%, and metallization rate of 89.97%.
Embodiment 3
[0032] A. Mix the oxidized slag and iron concentrate at a mass percentage of 45:55, and mix them evenly in the proportion of iron raw material 75%, coke powder 22%, and quicklime 3%.
[0033] B. Spread the raw materials prepared in the above step A in a loose shape on the material tray, the height of the material layer is 30mm, after the material tray is pushed into the microwave pusher kiln, the temperature is raised to 1050°C, reduced for 160min, and ventilated for 10s every 15min, and then cooled out Iron and iron slag are separated to obtain direct reduced iron products with TFe90.98%, MFe83.28%, and metallization rate of 91.54%.
[0034] The push plate kiln is powered by 220V power supply, and has 6 groups of microwave sources, each group has 3 phases, each phase averages 12A, the total current is 216 A, and the power is 47.52 kW.
PUM
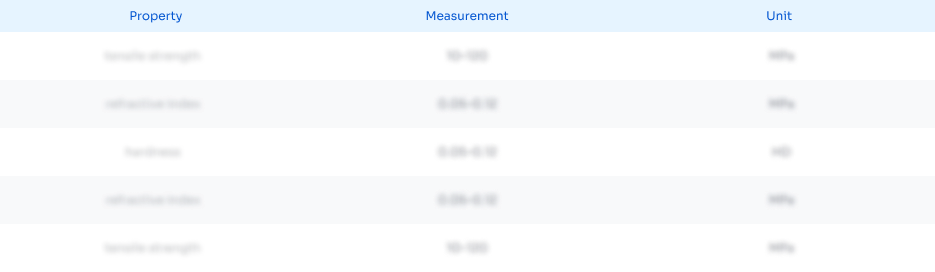
Abstract
Description
Claims
Application Information

- Generate Ideas
- Intellectual Property
- Life Sciences
- Materials
- Tech Scout
- Unparalleled Data Quality
- Higher Quality Content
- 60% Fewer Hallucinations
Browse by: Latest US Patents, China's latest patents, Technical Efficacy Thesaurus, Application Domain, Technology Topic, Popular Technical Reports.
© 2025 PatSnap. All rights reserved.Legal|Privacy policy|Modern Slavery Act Transparency Statement|Sitemap|About US| Contact US: help@patsnap.com