Preparation method of kaolin having high colloid index
A kaolin and colloidal price technology, applied in chemical instruments and methods, inorganic chemistry, non-metallic elements, etc., can solve problems such as difficult to meet the high colloidal price requirements of kaolin
- Summary
- Abstract
- Description
- Claims
- Application Information
AI Technical Summary
Problems solved by technology
Method used
Examples
Embodiment 1
[0024] A preparation method of high colloidal price kaolin, comprising the following steps,
[0025] (1) Dispersion by pulping: dissolve and disperse kaolin in water, then add dispersant to fully stir and disperse to obtain base material, enhance the dispersibility of kaolin in water, improve gloss, improve coloring power and hiding power, improve color development and performance Toning property, prevent floating color, prevent flocculation, prevent sedimentation; the dispersant in this embodiment is one or more of sodium hexametasulfate, sodium pyrophosphate and organic polypropylene;
[0026] (2) Desanding and impurity removal: the base material is successively passed through the grit chamber and the spiral grading and desandering machine for desanding to remove coarse-grained impurities to obtain the primary pulp material;
[0027] (3) Bleaching treatment: transport the raw pulp material to the mixing tank, add sulfuric acid solution and sodium dithionite solution, adjust ...
Embodiment 2
[0032] A kind of preparation method of high colloidal price kaolin of the present embodiment comprises the following steps,
[0033] (1) Pulping and dispersion: dissolve and disperse kaolin in water, then add a dispersant to fully stir and disperse to obtain a base material; the dispersant in this example is one of sodium hexametasulfate, sodium pyrophosphate and organic polypropylene or two or more;
[0034] (2) Desanding and impurity removal: the base material is successively passed through the grit chamber and the spiral grading and desandering machine for desanding to remove coarse-grained impurities to obtain the primary pulp material;
[0035] (3) Magnetic separation to remove iron, using a magnet to absorb and remove the iron minerals from the primary slurry;
[0036] (4) Bleaching treatment: transport the raw material of the ore pulp after the magnetic separation and iron removal step to the stirring tank, add sulfuric acid solution and sodium dithionite solution, adj...
Embodiment 3
[0041] The difference between the preparation method of a high colloidal price kaolin in this example and Example 1 is that the step (4) of this example is modified with ammonia water, the mass percentage concentration of ammonia water is 10%, and the amount of ammonia water added is Add 0.15kg of ammonia water per ton of pulp concentrate, and the stirring time is 15min. Other steps and principles of this embodiment are the same as those of Embodiment 1, and will not be repeated here.
PUM
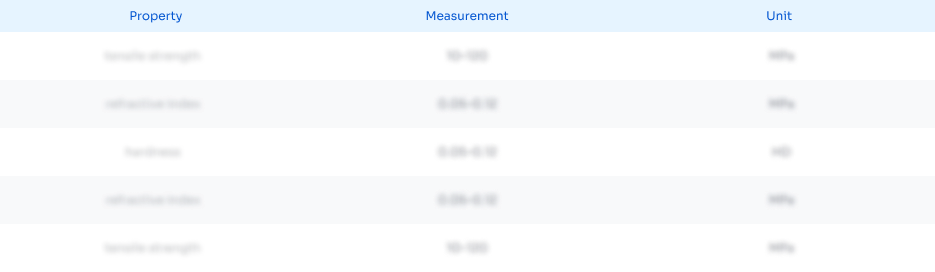
Abstract
Description
Claims
Application Information

- R&D
- Intellectual Property
- Life Sciences
- Materials
- Tech Scout
- Unparalleled Data Quality
- Higher Quality Content
- 60% Fewer Hallucinations
Browse by: Latest US Patents, China's latest patents, Technical Efficacy Thesaurus, Application Domain, Technology Topic, Popular Technical Reports.
© 2025 PatSnap. All rights reserved.Legal|Privacy policy|Modern Slavery Act Transparency Statement|Sitemap|About US| Contact US: help@patsnap.com