Method of recovering barite from waste drilling mud
A drilling mud, barite technology, applied in the direction of calcium/strontium/barium sulfate, etc., can solve the problems of incomplete separation and high operating costs, and achieve the effects of low cost and improved efficiency
- Summary
- Abstract
- Description
- Claims
- Application Information
AI Technical Summary
Problems solved by technology
Method used
Examples
Embodiment 1
[0021] Shengli Oilfield waste drilling mud 150m3, after removing the larger debris, use a 20-mesh sieve to separate the larger drilling cuttings in the mud, add sulfuric acid with a concentration of 30% in the reaction kettle, and fully stir, When the pH value of the cuttings reaches 6, add appropriate amount of water to control the density of the mud at 1.25g / ml, add 150kg of water glass, 45kg of oleic acid, 45kg of sodium dodecylsulfonate, and 15kg of citric acid, and then stir Under the conditions, the mud is introduced into the flotation tank for flotation. After 5 days, 47 tons of barite powder are obtained, and 50kg of polyethylene glycol and 100kg of quaternary ammonium salt are added for modification to obtain reusable barite powder. The purity of spar powder is 95%.
Embodiment 2
[0023] The waste drilling mud of Shengli Oilfield is 210m3. After removing the larger debris, the larger cuttings in the mud are separated by sieve with 20 meshes. When the pH value of the cuttings reaches 6.5, add appropriate amount of water to control the density of the mud at 1.3g / ml, add 210kg of water glass, 90kg of oleic acid, 50kg of sodium dodecylsulfonate, and 20kg of citric acid, and then stir Under the conditions, the mud is introduced into the flotation tank for flotation. After 5 days, 61 tons of barite powder are obtained, and 60kg of polyethylene glycol and 60kg of quaternary ammonium salt are added for modification to obtain reusable barite powder. The purity of stone powder is 94%.
Embodiment 3
[0025] Huabei oilfield waste drilling mud 100m3, after removing the larger debris, use a 20-mesh sieve to separate the larger drilling cuttings in the mud, add sulfuric acid with a concentration of 25% in the reaction kettle, and fully stir, When the pH value of the cuttings reaches 6, add an appropriate amount of water to control the density of the mud at 1.27g / ml, add 120kg of water glass, 50kg of oleic acid, 40kg of sodium dodecylsulfonate, and 10kg of citric acid, and then stir Under the conditions, the mud is introduced into the flotation tank for flotation. After 7 days, 25 tons of barite powder are obtained, and 30kg of polyethylene glycol and 60kg of quaternary ammonium salt are added for modification to obtain reusable barite powder. The purity of stone powder is 95%.
PUM
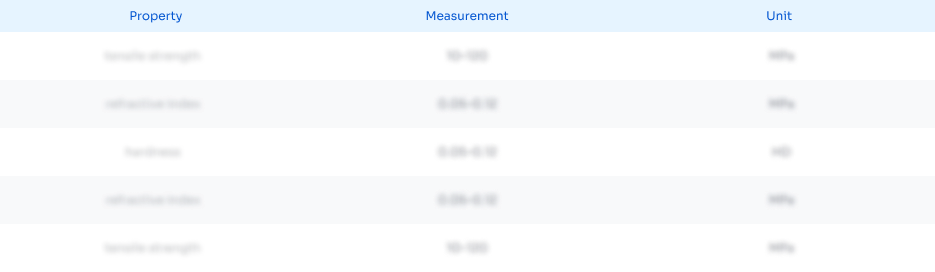
Abstract
Description
Claims
Application Information

- R&D
- Intellectual Property
- Life Sciences
- Materials
- Tech Scout
- Unparalleled Data Quality
- Higher Quality Content
- 60% Fewer Hallucinations
Browse by: Latest US Patents, China's latest patents, Technical Efficacy Thesaurus, Application Domain, Technology Topic, Popular Technical Reports.
© 2025 PatSnap. All rights reserved.Legal|Privacy policy|Modern Slavery Act Transparency Statement|Sitemap|About US| Contact US: help@patsnap.com