Grinding method for forming small-hole thread of hard and brittle material
A technology for forming and grinding hard and brittle materials, used in metal processing equipment, tangent devices, manufacturing tools, etc., can solve the problems of thread surface scratches, low processing efficiency, wear strength, etc., and achieve good thread surface quality and high machining. Efficiency and the effect of ensuring thread machining accuracy
- Summary
- Abstract
- Description
- Claims
- Application Information
AI Technical Summary
Problems solved by technology
Method used
Image
Examples
Embodiment
[0028] Example: M2 small hole thread processing is carried out on the silicon carbide particle-reinforced aluminum matrix composite material, and the processing thread precision is required to be grade 4.
[0029] Diamond or CBN abrasives can be used for disc shaped grinding wheels.
[0030] According to the requirements of the embodiment, it can be seen that the nominal diameter of the M2 internal thread is D=2, and the pitch P=0.4; the actual processing error threshold (four-level accuracy) of the M2 thread is δ o is 0.056mm, put the above value into the formula (1), let the formula (1) take the equal sign, the critical value of the coefficient η [η]=0.23 can be obtained.
[0031] When η≤[η], that is, η≤0.23, d=ηD≤0.46, the disc-shaped forming grinding wheel can meet the processing requirements without modification. When [η]o -Δα, where α o Is the standard thread angle, usually 60 °. Δα is the modification angle of the disc-shaped forming grinding wheel. According to the ...
PUM
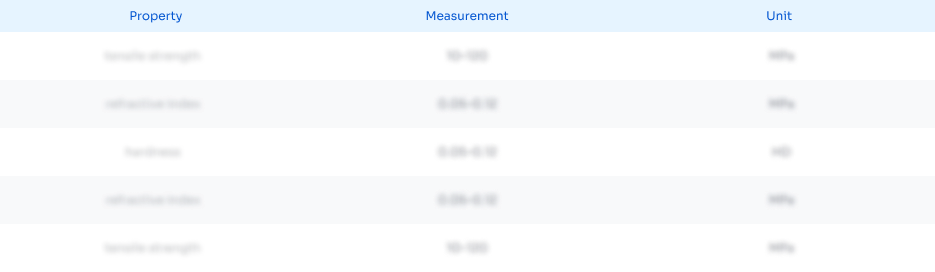
Abstract
Description
Claims
Application Information

- R&D
- Intellectual Property
- Life Sciences
- Materials
- Tech Scout
- Unparalleled Data Quality
- Higher Quality Content
- 60% Fewer Hallucinations
Browse by: Latest US Patents, China's latest patents, Technical Efficacy Thesaurus, Application Domain, Technology Topic, Popular Technical Reports.
© 2025 PatSnap. All rights reserved.Legal|Privacy policy|Modern Slavery Act Transparency Statement|Sitemap|About US| Contact US: help@patsnap.com