A Design Method for Composite Airfoil Fan Blades
A technology of airfoil blade and design method, which is applied in the direction of mechanical equipment, machine/engine, liquid fuel engine, etc., can solve the problems of high mold investment cost, low operating efficiency, high noise, etc. Effect
- Summary
- Abstract
- Description
- Claims
- Application Information
AI Technical Summary
Problems solved by technology
Method used
Image
Examples
Embodiment 1
[0031] Example 1: Generation of Composite Airfoil
[0032] Composite airfoil generation mode of the present invention is divided into following six categories:
[0033] ① Leading edge superimposed compound airfoil: the standard airfoil is used as the main body of the airfoil blade, and the leading edge of the main body of the airfoil blade is extended to superimpose the airfoil so that the superimposed airfoil coincides with the pressure surface line of the main body of the airfoil blade, that is wing
[0034] The radius of curvature of the pressure surface of the main body of the airfoil and the radius of curvature of the pressure surface of the superimposed airfoil are tangent at the joint point, the maximum thickness of the superimposed airfoil is smaller than the maximum thickness of the main body of the airfoil, and the main body of the airfoil is Smooth transition between profile and superimposed airfoil profiles.
[0035] ②Composite airfoil superimposed on the trailin...
Embodiment 2
[0039] ⑥ Composite airfoil superimposed on the suction surface: the standard airfoil is used as the main body of the airfoil blade, and the airfoil is superimposed on the suction surface of the subject airfoil. On the suction surface, the main shape line of the airfoil blade and the superimposed airfoil shape line are smoothly transitioned. Embodiment 2: select the type of composite airfoil, and determine the section form
[0040] (1) Determine the airfoil profile line using the composite airfoil according to the engineering calculation flow pattern.
[0041] (2) The section size of the composite airfoil is not large, or the solid structure of the composite airfoil can be selected when considering the conditions of blade wear resistance, strength, and stiffness, etc.
[0042] (3) When the section size of the composite airfoil is large, different forms of hollow section structures can be selected under the conditions of blade strength and stiffness.
[0043] (4) When the sect...
Embodiment 3
[0044] Example 3: blade profile material
[0045] According to the different media (occasions) applicable to the impeller blades, different materials are selected. The blade material can be metallic material, non-metallic material, composite material.
PUM
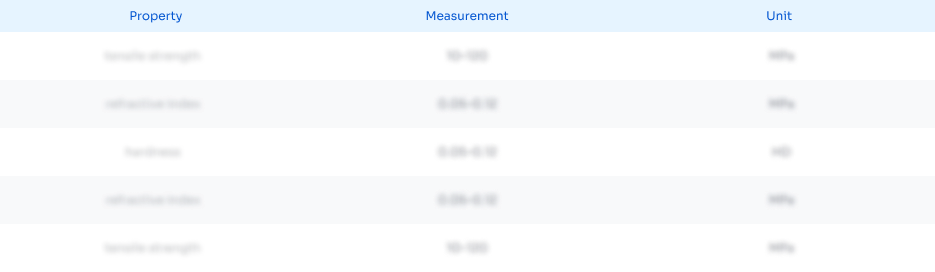
Abstract
Description
Claims
Application Information

- R&D
- Intellectual Property
- Life Sciences
- Materials
- Tech Scout
- Unparalleled Data Quality
- Higher Quality Content
- 60% Fewer Hallucinations
Browse by: Latest US Patents, China's latest patents, Technical Efficacy Thesaurus, Application Domain, Technology Topic, Popular Technical Reports.
© 2025 PatSnap. All rights reserved.Legal|Privacy policy|Modern Slavery Act Transparency Statement|Sitemap|About US| Contact US: help@patsnap.com