Production method of grinding wheel for steel tube
A manufacturing method and technology of grinding wheels, applied in the field of grinding wheels, to achieve high linear speed, reduce raw material costs, and improve compressive strength
- Summary
- Abstract
- Description
- Claims
- Application Information
AI Technical Summary
Problems solved by technology
Method used
Image
Examples
Embodiment 1
[0008] F12 zirconium corundum and F14 brown corundum are selected as abrasives, and the weight ratio of each raw material is: 35 parts of F12 zirconium corundum, 65 parts of F14 brown corundum, 20 parts of phenolic resin, 5 parts of pyrite, 1 part of feldspar, and cryolite 3 parts, 1 part of carbon black, and 4 parts of gypsum; accurately weigh the above-mentioned various raw materials, pour them into an S-type mixer and mix for half an hour, then discharge, sieve and set aside. The size of the grinding wheel pressed on the hydraulic press is 1-400×50×127, and the unit weight of each grinding wheel is 14.4kg. There is a raised special scraper to scrape flat, and a groove concentric with the die ring and mandrel is formed in the non-grinding area. The center distance of the groove is 240mm, and a ¢240mm steel ring is placed in the groove; the second cast For the molding material weighing 4.8 kg, repeat the above operation and place a steel ring of the same size; throw the moldi...
Embodiment 2
[0012] F10 zirconium corundum and F12 brown corundum are selected as abrasives, and the weight ratio of each raw material is: 40 parts of F12 zirconium corundum, 60 parts of F14 brown corundum, 23 parts of phenolic resin, 7 parts of pyrite, 2 parts of feldspar, cryolite 2 parts, 3 parts of carbon black, and 3 parts of gypsum; accurately weigh the above-mentioned various raw materials, pour them into a cone mixer and mix for half an hour, then discharge, sieve and set aside. The size of the grinding wheel pressed on the hydraulic press is 1-250×40×32, and the unit weight of each grinding wheel is 4.8kg. There is a raised special scraper to scrape flat, and form a groove concentric with the die ring and mandrel in the non-grinding area. The center distance of the groove is 120mm, and a ¢120mm steel ring is placed in the groove; the second cast For the molding material weighing 1.6 kg, repeat the above operation and place a steel ring of the same size; throw the molding material ...
PUM
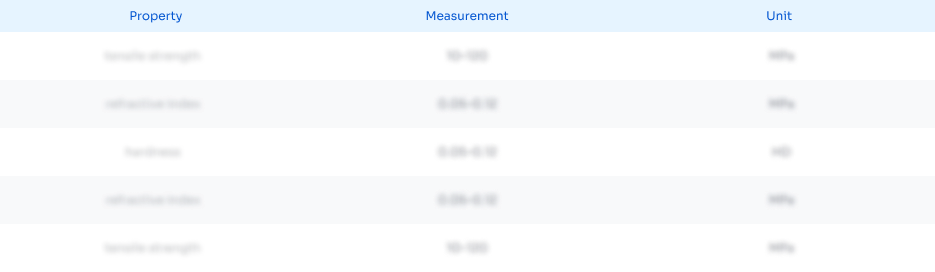
Abstract
Description
Claims
Application Information

- R&D
- Intellectual Property
- Life Sciences
- Materials
- Tech Scout
- Unparalleled Data Quality
- Higher Quality Content
- 60% Fewer Hallucinations
Browse by: Latest US Patents, China's latest patents, Technical Efficacy Thesaurus, Application Domain, Technology Topic, Popular Technical Reports.
© 2025 PatSnap. All rights reserved.Legal|Privacy policy|Modern Slavery Act Transparency Statement|Sitemap|About US| Contact US: help@patsnap.com