Double-calcination process of sulfuric acid and rare earth concentrate rotary kiln calcination device
A rare earth sulfate, roasting device technology, applied in waste heat treatment, lighting and heating equipment, furnace components and other directions, can solve the problems of difficult waste gas treatment technology, high investment and operating costs, waste of radioactive thorium resources, etc. The effect of processing, improving the utilization rate of heat energy and improving the utilization rate of resources
- Summary
- Abstract
- Description
- Claims
- Application Information
AI Technical Summary
Problems solved by technology
Method used
Image
Examples
Embodiment 1
[0037] As shown in the figure; the outlet end of the low-temperature roasting kiln 13 is set above the inlet end of the high-temperature roasting kiln 17, the feed smoke chamber 12 is set at the inlet end of the low-temperature roast kiln 13, the inlet is arranged above the feed smoke chamber 12, and the top of the feed smoke chamber 12 Set the feeding system, the dry powder bin 8 is set under the gas-solid separator 7 of the low temperature system of the feeding system, the dry powder metering scale 9 is set under the outlet of the dry powder bin 8, and the agitator 10 is set under the dry powder metering scale 9, and the agitator 10- A sulfuric acid metering system 11 is installed on the side, and a pipeline is arranged between the agitator 10 and the sulfuric acid metering system 11. The lower part of the outlet of the agitator 10 corresponds to the inlet of the low-temperature roasting kiln 13 feeding fume chamber 12; the side of the feeding fume chamber 12 inlet A dispersi...
Embodiment 2
[0039] As shown in the figure; low-temperature kiln combustion system 14 is set in the middle of the outlet end of low-temperature roasting kiln 13, high-temperature kiln combustion system 18 is set in the middle of the outlet end of high-temperature roasting kiln 17, and smoke is set between the outlet end of high-temperature roasting kiln 17 and the outlet end of low-temperature roasting kiln 13. Gas discharge pipeline; the outlet of the low-temperature roasting kiln 13 is corresponding to the import of the high-temperature roasting kiln 17 to set the material pipeline, and the side of the high-temperature roasting kiln 17 inlet is provided with a high-temperature system gas-solid separator 20, and the delivery nozzle above the high-temperature roasting kiln 17 inlet is connected to the high-temperature Pipelines are arranged between the gas-solid separators 20 of the system; an inlet is arranged below the inlet side of the high-temperature roasting kiln 17, and an outlet is a...
Embodiment 3
[0040] The roasting temperature of the low-temperature roasting kiln 13 of the rotary kiln roasting rare earth concentrate of sulfuric acid in the present invention is between 200°C and 500°C. After ~450°C, it is discharged into the high-temperature nozzle above the dispersing dryer 6 through the pipeline, and the waste gas entering the dispersing dryer 6 through the high-temperature nozzle is dispersed and suspended for heat exchange with rare earth and iron powder. A pipeline is set between another conveying nozzle on the top and the gas-solid separator 7 of the low-temperature system. When the rare earth and iron powder in the dryer 6 are dispersed to become suspended solids, they enter the gas-solid separator 7 of the low-temperature system through the pipeline for gas-solid separation. Solid separation, the separated gas enters the low-temperature system dust collector 15 through the pipeline above the low-temperature system gas-solid separator 7 for dust removal, and the ...
PUM
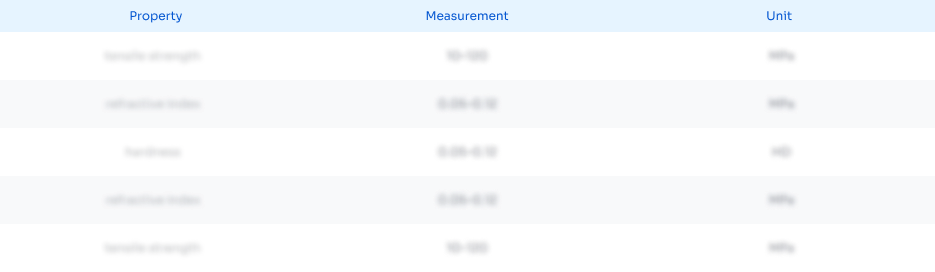
Abstract
Description
Claims
Application Information

- R&D
- Intellectual Property
- Life Sciences
- Materials
- Tech Scout
- Unparalleled Data Quality
- Higher Quality Content
- 60% Fewer Hallucinations
Browse by: Latest US Patents, China's latest patents, Technical Efficacy Thesaurus, Application Domain, Technology Topic, Popular Technical Reports.
© 2025 PatSnap. All rights reserved.Legal|Privacy policy|Modern Slavery Act Transparency Statement|Sitemap|About US| Contact US: help@patsnap.com