Numerical control equipment
A numerical control equipment and guide technology, applied in metal processing equipment, large fixed members, feeding devices, etc., can solve the problems of fast wear of moving parts, affecting processing accuracy, inaccurate positioning, etc., and achieve good guiding effect
- Summary
- Abstract
- Description
- Claims
- Application Information
AI Technical Summary
Problems solved by technology
Method used
Image
Examples
Embodiment 1
[0022] Such as Figure 1 to Figure 4 As shown, a numerical control device includes a main body frame 1 and a workbench 2 integrally formed. The main body frame 1 includes a square base 3, which is integrally formed with the base 3 and is arranged at the four corners of the base 3 and the main support columns 4 respectively arranged at the middle positions of the left side, the right side and the rear side of the base, connecting the main support columns 4 Between horizontal connecting column 5. The main support frame 6 arranged on the main support column 4 is integrally formed with the main support column 4 . The main support frame 6 is a square closed-loop structure with an opening facing the vertical direction.
[0023] It also includes the X-direction sliding seat 7. Between the main support frame 6 and the X-direction sliding seat 7, there are mutually matched X forward guide rails and X backward guide rails. The X slide seat 7 can slide back and forth along the X forw...
Embodiment 2
[0038] Such as Figure 5 As shown, a numerical control device is different from Embodiment 1 in that a main shaft 61 is installed in the Z guide rod 60, the tool holder 62 of the main processing head is directly fixed on the main shaft 60, and the tool 63 is fixed on the tool holder. Head 62 on.
[0039] In the present invention, the main processing head may be provided with a tool clamping head, or the main processing head may be a paint spraying head, a welding gun, a laser gun, a plasma cutting gun, a screw gun or a gas cutting gun. When a milling cutter is installed on the tool chuck, the function of milling can be realized; when a grinding wheel is installed on the tool chuck, the function of grinding can be realized; when a boring tool is installed on the tool chuck , the function of boring can be realized; when the drill bit is installed on the tool holder, the function of drilling can be realized; when the main processing head is a painting head, the function of spray...
PUM
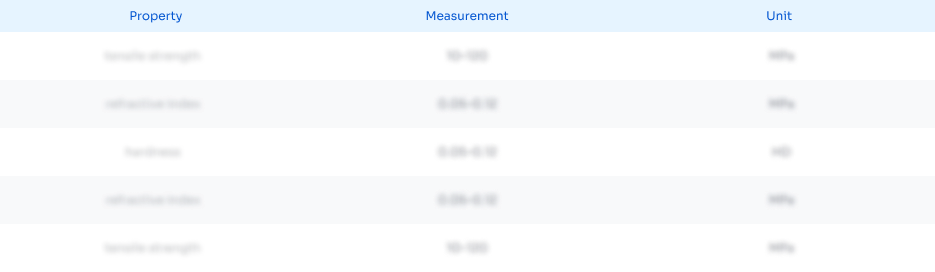
Abstract
Description
Claims
Application Information

- R&D Engineer
- R&D Manager
- IP Professional
- Industry Leading Data Capabilities
- Powerful AI technology
- Patent DNA Extraction
Browse by: Latest US Patents, China's latest patents, Technical Efficacy Thesaurus, Application Domain, Technology Topic, Popular Technical Reports.
© 2024 PatSnap. All rights reserved.Legal|Privacy policy|Modern Slavery Act Transparency Statement|Sitemap|About US| Contact US: help@patsnap.com