Multi-stage premixed compression ignition method for gasoline fuels with low octane value
A multi-stage premixed compression ignition, low octane number technology, applied in fuel injection control, engine control, machine/engine, etc., can solve the problems of inability to widen direct control, high nitrogen oxide emissions, difficult heat release process, etc. Achieve the effect of soft and controllable low-polluting combustion process, low fuel consumption and low production cost
- Summary
- Abstract
- Description
- Claims
- Application Information
AI Technical Summary
Problems solved by technology
Method used
Image
Examples
Embodiment 1
[0030] Use naphtha as fuel without adding anti-knock agents. The parameters of the engine used in the embodiment are: cylinder bore 83.1 mm, stroke 92 mm, connecting rod length 145.8 mm, compression ratio 16.7, intake valve closing time -130° CAATDC (relative to compression top dead center).
[0031] Electronically controlled high-voltage common rail system controls operation. When the engine speed is 2000r / mim and the load is 0.7MPa IMEP (average indicated pressure), the timing of naphtha injection is: the first injection is 80°CA before the compression top dead center, and the second injection is after the compression top dead center 5°CA (see figure 1 ), the injection pressure is 80MPa. Do two injections - burn. The proportion of fuel injection is 50% of the total fuel mass of the first injection cycle, and 50% of the total fuel mass of the second injection cycle. There is no overlap between the injection process and the combustion process. The indicated efficiency of ...
Embodiment 2
[0033] Use naphtha as fuel without adding anti-knock agents. The parameters of the engine used in the embodiment are: cylinder bore 83.1 mm, stroke 92 mm, connecting rod length 145.8 mm, compression ratio 16.7, intake valve closing time -130° CAATDC (relative to compression top dead center).
[0034] Electronically controlled high-voltage common rail system controls operation. When the engine speed is 1500r / mim and the load is 0.6MPa IMEP (average indicated pressure), the timing of naphtha injection is: the first injection is 40°CA before the compression top dead center, and the second injection is after the compression top dead center 5°CA, the injection pressure is 80MPa. Do two injections - burn. The proportion of fuel injection is 50% of the total fuel mass of the first injection cycle, and 50% of the total fuel mass of the second injection cycle. There is no overlap between the injection process and the combustion process. The indicated efficiency of this engine is 43...
PUM
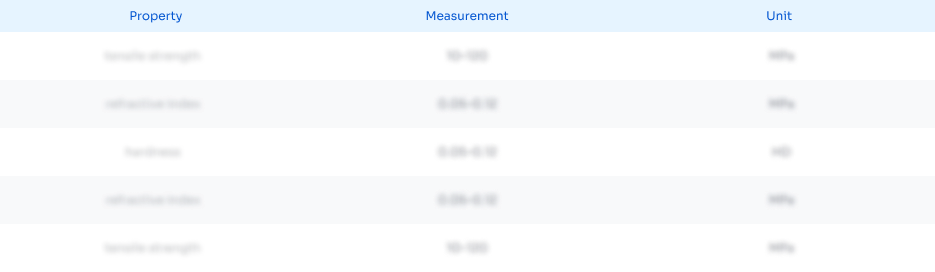
Abstract
Description
Claims
Application Information

- R&D
- Intellectual Property
- Life Sciences
- Materials
- Tech Scout
- Unparalleled Data Quality
- Higher Quality Content
- 60% Fewer Hallucinations
Browse by: Latest US Patents, China's latest patents, Technical Efficacy Thesaurus, Application Domain, Technology Topic, Popular Technical Reports.
© 2025 PatSnap. All rights reserved.Legal|Privacy policy|Modern Slavery Act Transparency Statement|Sitemap|About US| Contact US: help@patsnap.com