High-magnesium minimum-inflation low-heat cement and preparation method thereof
A low-heat cement and micro-expansion technology, applied in the field of cement, can solve the problems of low heat of hydration, low dry shrinkage, concrete cracks, etc., and achieve the effects of low cost, reduced concrete cracks, and simple production process
- Summary
- Abstract
- Description
- Claims
- Application Information
AI Technical Summary
Problems solved by technology
Method used
Image
Examples
Embodiment 2
[0028] The mineral composition of the high-magnesium micro-expansion low-heat cement clinker listed in Example 2 is (percentage by weight): C 3 S (tricalcium silicate) 27.66%, C 2 S (dicalcium silicate) 48.04%, C 3 A (tricalcium aluminate) 2.79%, C 4 AF (tetracalcium aluminoferrite) 14.92%; MgO content in cement clinker is 6.71%. This scheme can be regarded as the most preferred.
[0029] Although the above lists the specific values of each optimal scheme according to Table 2, it can be understood that the listed data changes according to the change of the composition of cement raw materials in actual application, and the fluctuation of the change is normal within the range of ±10%. .
[0030] In the above-mentioned high-magnesium micro-expansion low-heat cement clinker, the proportion of raw materials for forming the mineral composition is (weight percent): 50-80% of calcareous raw materials, 5-30% of clay-based raw materials, 0-10% of iron powder, industrial waste resi...
Embodiment 1-5
[0036] Embodiment 1-5, preparation of high-magnesium micro-expansion low-heat cement
[0037] The raw material formula of the high-magnesium micro-expansion low-heat cement of the embodiment of the present invention 1-5 is as shown in table 1:
[0038] The raw material formula (unit: weight percent) of high-magnesium micro-expansion low-heat cement of table 1
[0039]
[0040] High-activity high-magnesium micro-expansion low-heat cement clinker is produced by conventional methods in a φ2.5×45m five-stage cyclone preheater kiln. The clinker is fine and uniform, with good granulation and no pulverization; The raw material is mixed with gypsum as a retarder to produce high-magnesium micro-expansion low-heat cement.
[0041] See Table 2 for the chemical analysis, rate and mineral composition of the cement clinker prepared in Examples 1-5 and the reference cement.
[0042] Table 2 Chemical analysis, ratio and mineral composition of high-magnesium micro-expansion low-heat cemen...
PUM
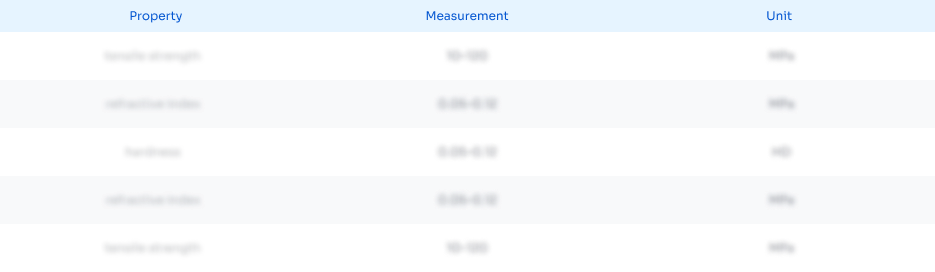
Abstract
Description
Claims
Application Information

- R&D Engineer
- R&D Manager
- IP Professional
- Industry Leading Data Capabilities
- Powerful AI technology
- Patent DNA Extraction
Browse by: Latest US Patents, China's latest patents, Technical Efficacy Thesaurus, Application Domain, Technology Topic, Popular Technical Reports.
© 2024 PatSnap. All rights reserved.Legal|Privacy policy|Modern Slavery Act Transparency Statement|Sitemap|About US| Contact US: help@patsnap.com