Preparation method of vegetable carbon plastic composites
A composite material and plant charcoal technology, which is applied in the field of preparation of plant charcoal plastic composite materials, can solve the problems of mechanical properties, flame retardancy and antistatic properties that need to be improved, and high requirements for flame retardancy, and achieve good electrical conductivity and deodorization functions , Improve processing performance, antistatic promotion effect
- Summary
- Abstract
- Description
- Claims
- Application Information
AI Technical Summary
Problems solved by technology
Method used
Image
Examples
Embodiment 1
[0039] The plant material used in this embodiment is corn cob.
[0040] Put the plant raw materials into a microwave vacuum tank, evacuate to a vacuum of -0.02MPa, and then perform microwave treatment, the microwave frequency is 300MHz, and the microwave treatment time is 1min;
[0041] The plant raw materials obtained through pre-treatment are successively dried, pre-carbonized, carbonized, calcined and cooled. The temperature of each temperature measurement point is 150°C in drying zone A, 275°C in pre-carbonization zone B, and 450°C in carbonization zone C. Observe when heating up figure 1 The D zone shown is the temperature at different locations in the combustion zone. When the temperature in the combustion zone, such as d2, is too low, open the small hole in the combustion zone and introduce air to burn on the spot to increase the temperature in the area and control the bamboo to move down. For the combustion zone temperature experienced during the process, control the combu...
Embodiment 2
[0047] The plant material used in this embodiment is bamboo (about 40 cm in length).
[0048] Put the plant raw materials into a microwave vacuum tank, evacuate to a vacuum of -0.001MPa, and then perform microwave treatment, the microwave frequency is 950MHz, and the microwave treatment time is 3min;
[0049] The plant raw materials obtained through pre-treatment are successively dried, pre-carbonized, carbonized, calcined and cooled. The temperature of each temperature measurement point is 150°C in drying zone A, 275°C in pre-carbonization zone B, and 450°C in carbonization zone C. Observe when heating up figure 1 The D zone shown is the temperature at different locations in the combustion zone. When the temperature in the combustion zone, such as d2, is too low, open the small hole in the combustion zone and introduce air to burn on the spot to increase the temperature in the area and control the bamboo to move down. For the combustion zone temperature experienced during the pro...
Embodiment 3
[0054] The plant raw material used in this embodiment is pine, and the pine is first cut after removing the skin impurities, and the length is controlled not to exceed 15 cm.
[0055] Feed the plant raw materials into a microwave vacuum tank, evacuate to a vacuum of -0.01MPa, and then perform microwave treatment, the microwave frequency is 550MHz, and the microwave treatment time is 2min;
[0056] The plant raw materials obtained through pre-treatment are dried, pre-carbonized, carbonized, calcined and cooled in sequence. The temperature of each temperature measurement point is 180°C in drying zone A, 325°C in pre-carbonization zone B, and 530°C in carbonization zone C. Observe when heating up figure 1 The D zone shown is the temperature at different locations in the combustion zone. When the temperature in the combustion zone, such as d2, is too low, open the small hole in the combustion zone and introduce air to burn on the spot to increase the temperature in the area and control...
PUM
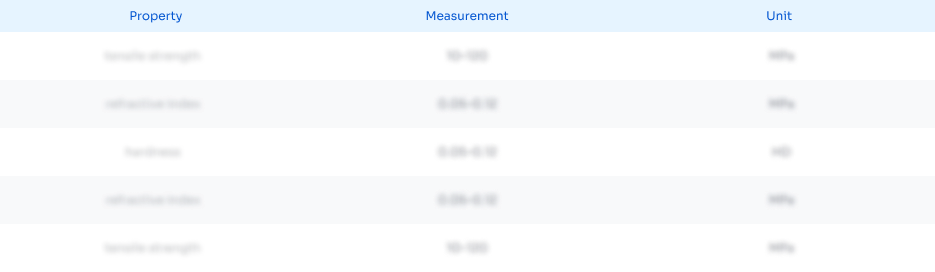
Abstract
Description
Claims
Application Information

- R&D
- Intellectual Property
- Life Sciences
- Materials
- Tech Scout
- Unparalleled Data Quality
- Higher Quality Content
- 60% Fewer Hallucinations
Browse by: Latest US Patents, China's latest patents, Technical Efficacy Thesaurus, Application Domain, Technology Topic, Popular Technical Reports.
© 2025 PatSnap. All rights reserved.Legal|Privacy policy|Modern Slavery Act Transparency Statement|Sitemap|About US| Contact US: help@patsnap.com