Preparation method of flame-retardant core-shell-type acrylic resin
A core-shell type, acrylic technology, applied in coatings, textiles, papermaking, fiber treatment, etc., can solve the problems of poor flame retardancy, achieve good compatibility, low price, and improve flame resistance
- Summary
- Abstract
- Description
- Claims
- Application Information
AI Technical Summary
Problems solved by technology
Method used
Examples
example 1
[0024] (1) Add 50g of deionized water, 0.33g of emulsifier sodium lauryl sulfate and fatty alcohol polyoxyethylene ether (the type of fatty alcohol polyoxyethylene ether is OS-15, non-ionic type, purchased from Jiangsu Haian Petrochemical Plant, the same below) 0.17g, methacrylic acid 0.3g, raise the reaction temperature to 40°C, stir for 15min, add A monomer, and emulsify for 30min. When the temperature rises to 70°C, reflux water is passed, and when the temperature reaches 75°C, 0.2 g of potassium persulfate is added dropwise for 1 hour, followed by a heat preservation reaction for 3 hours, 1 g of dimethyl methyl phosphonate is added dropwise, and the reaction time is 1 hour to obtain a nucleus layer emulsion;
[0025] A monomer and its dosage: A monomer is composed of 6g of butyl acrylate, 4g of methyl methacrylate and 2.5g of ethyl acrylate;
[0026] (2) Add B monomer and potassium persulfate 0.3g dropwise to the core layer emulsion at the same time, dropwise adding time ...
example 2
[0029] (1) Add 70g of deionized water, 1.2g of emulsifier sodium lauryl sulfate, 0.6g of fatty alcohol polyoxyethylene ether, and 3.0g of methacrylic acid into the three-necked flask, raise the reaction temperature to 40°C, and stir for 15 minutes. Add A monomer, emulsification time 45min. When the temperature rises to 70°C, flow back water, and when the temperature reaches 75°C, start to add 0.4g of ammonium persulfate dropwise for 3 hours, keep warm for 5 hours, add 3g of dimethyl phosphite dropwise, and react for 3 hours to obtain a core layer emulsion ;
[0030] A monomer and its dosage: A monomer is composed of 8g of butyl acrylate, 6g of methyl methacrylate and 3.5g of ethyl acrylate;
[0031] (2) Add B monomer and ammonium persulfate 0.5g dropwise to the core layer emulsion at the same time, dropwise for 3h, 85°C for 2h, add calcium-based bentonite dispersion 20g, keep warm for 3h, then drop three Methylolpropane trimethacrylate 1.0g, keep warm for 2 hours, cool down ...
example 3
[0034] (1) Add 60g of deionized water, 0.8g of emulsifier sodium lauryl sulfate, 0.4g of fatty alcohol polyoxyethylene ether, and 1.7g of methacrylic acid into the three-necked flask, raise the reaction temperature to 40°C, and stir for 15min. Add A monomer, and the emulsification time is 35min. When the temperature rises to 70°C, reflux water is passed, and when the temperature reaches 75°C, 0.3g of ammonium persulfate is added dropwise, the dropwise addition time is 2h, the heat preservation reaction is 4h, and 2g of trimethylsilylmethylphosphonic acid dimethyl is added dropwise, and the reaction time is 2h , to obtain the core layer emulsion;
[0035] A monomer and its dosage: A monomer is composed of 7g of butyl acrylate, 5g of methyl methacrylate and 3.0g of ethyl acrylate;
[0036] (2) Add B monomer and ammonium persulfate 0.4g dropwise to the core layer emulsion at the same time, add dropwise for 2 hours, keep warm for 2 hours at 80°C, add 15g of calcium-based bentonit...
PUM
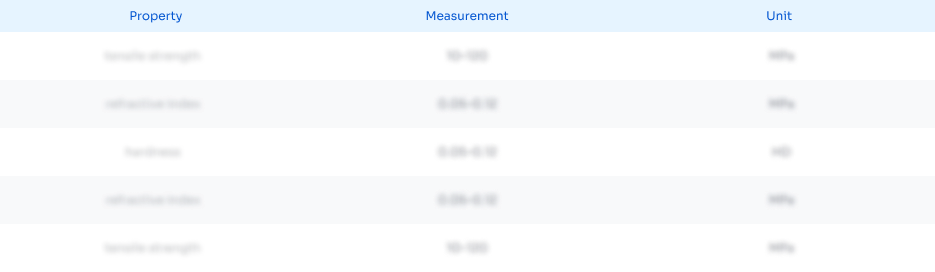
Abstract
Description
Claims
Application Information

- R&D Engineer
- R&D Manager
- IP Professional
- Industry Leading Data Capabilities
- Powerful AI technology
- Patent DNA Extraction
Browse by: Latest US Patents, China's latest patents, Technical Efficacy Thesaurus, Application Domain, Technology Topic, Popular Technical Reports.
© 2024 PatSnap. All rights reserved.Legal|Privacy policy|Modern Slavery Act Transparency Statement|Sitemap|About US| Contact US: help@patsnap.com