Compound filter material for high-temperature flue gas bag-type dust removal system and preparation method of same
A bag-type dust removal and high-temperature flue gas technology, applied in separation methods, chemical instruments and methods, filtration and separation, etc., can solve the problems of short service life of filter bags, poor high-temperature impact resistance, high thermal shrinkage, etc., and achieve service life Long, cost-effective, high-temperature strength stability and good dimensional stability
- Summary
- Abstract
- Description
- Claims
- Application Information
AI Technical Summary
Problems solved by technology
Method used
Image
Examples
preparation example Construction
[0027] The present invention also provides a method for preparing the composite filter material for the above-mentioned high-temperature flue gas bag-type dust removal system, comprising a step of pretreatment of polysulfone fiber, in the step of pretreatment of polysulfone fiber, Spray evenly on the polysulfone fibers with antistatic oil, balance for 4-10 hours; include a step of preparing a base fabric woven from blended yarns of polysulfone fibers and aramid fibers; include a step of preparing polysulfone fibers and aramid fibers The step of mixing fibers, in the step of preparing the mixed fibers of polysulfone fiber and aramid fiber, making the mixed fiber of polysulfone fiber and aramid fiber through an air-laid process; The upper and lower sides of the base fabric are respectively stacked with sulfonamide and aramid mixed fiber layers, and the preliminary pre-needling step also includes a step of passing at least two spunlaces to form a plain felt, and also includes a de...
Embodiment 1
[0034] A composite filter material for a high-temperature flue gas bag-type dust removal system. The upper and lower surfaces of the base fabric 1 woven from polysulfonamide and aramid blended yarns are reinforced by air-laid and needle-punched / spunlace Combining the composite process symmetrically punctures the mixed fiber layer of aramid sulfone fiber and aramid fiber.
[0035] The polysulfone fiber and aramid blended yarn comprises 20 parts by weight of the polysulfone fiber and 80 parts by weight of the aramid 1313 fiber, and the parts by weight are based on the polysulfone fiber and the aramid fiber in the blended yarn. A total of 100 parts by weight of Lun 1313 fiber.
[0036] The mixed fiber of polysulfone and aramid contains 20 parts by weight of polysulfone fiber and 80 parts by weight of aramid 1313 fiber, and the parts by weight are based on the content of polysulfone fiber and aramid 1313 in the mixed fiber. 100 parts by weight of fibers in total.
[0037] A comp...
Embodiment 2
[0044]A composite filter material for a high-temperature flue gas bag-type dust removal system. The upper and lower surfaces of the base fabric 1 woven from polysulfonamide and aramid blended yarns are reinforced by air-laid and needle-punched / spunlace Combining the composite process symmetrically punctures the mixed fiber layer of aramid sulfone fiber and aramid fiber.
[0045] The polysulfone fiber and aramid blended yarn comprises 50 parts by weight of the polysulfone fiber and 50 parts by weight of the aramid 1313 fiber, and the parts by weight are based on the polysulfone fiber and the aramid fiber in the blended yarn A total of 100 parts by weight of Lun 1313 fiber.
[0046] The mixed fiber of polysulfone and aramid contains 50 parts by weight of polysulfone fiber and 50 parts by weight of aramid 1313 fiber, and the parts by weight are based on the content of polysulfone fiber and aramid 1313 in the mixed fiber. 100 parts by weight of fibers in total.
[0047] A compos...
PUM
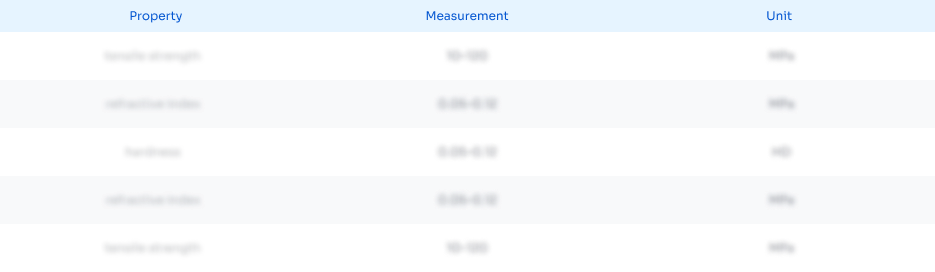
Abstract
Description
Claims
Application Information

- R&D
- Intellectual Property
- Life Sciences
- Materials
- Tech Scout
- Unparalleled Data Quality
- Higher Quality Content
- 60% Fewer Hallucinations
Browse by: Latest US Patents, China's latest patents, Technical Efficacy Thesaurus, Application Domain, Technology Topic, Popular Technical Reports.
© 2025 PatSnap. All rights reserved.Legal|Privacy policy|Modern Slavery Act Transparency Statement|Sitemap|About US| Contact US: help@patsnap.com