Method for preparing reduction carbon nano tube coated lithium iron phosphate cathode material
A technology of lithium ferrous phosphate and cathode material, applied in battery electrodes, electrical components, circuits, etc., can solve the problems of difficult control of nanotube growth efficiency, uneven distribution of carbon nanotubes, unstable electrochemical performance, etc. The effect of increased voltage platform, simple preparation process and good cycle performance
- Summary
- Abstract
- Description
- Claims
- Application Information
AI Technical Summary
Problems solved by technology
Method used
Image
Examples
Embodiment 1
[0030] 1) Preparation of carbon compounds
[0031] Mix citric acid and ethylene glycol in a molar ratio of 1:4, and stir at 45°C for 2 hours; place under the conditions of pressure of 10Pa and temperature of 125°C and stir for 5h to carry out the polymerization reaction; vacuum under the conditions of temperature of 175°C and pressure of 10Pa dry. The ethylene glycol that did not participate in the polymerization reaction was removed to obtain a brown mucus. The brown mucilage was placed in a tube furnace, heated to 300 °C isolated from air, and sintered at 300 °C for 3 hours; cooled to room temperature, and pulverized into a powdered precursor with a particle size of 20 meshes; the powdered precursor was placed in Al 2 O 3 In a porcelain boat, the carbon compounds were prepared by sintering at 400 °C for 8 h in an air atmosphere, and then naturally cooled to room temperature.
[0032] 2) Preparation of reduced carbon compounds
[0033] According to Na 2 SO 3 Weigh Na in...
Embodiment 2
[0037] 1) Preparation of carbon compounds
[0038] The citric acid and ethylene glycol were mixed according to the molar ratio of 1:4, stirred at 70 °C for 2 hours, placed under the conditions of a pressure of 10132 Pa and a temperature of 175 °C and stirred for 5 hours to carry out the polymerization reaction. Under the conditions of temperature 175 ℃ and pressure 1013Pa, vacuum drying to remove ethylene glycol that did not participate in the polymerization reaction to obtain brown mucilage; heat the brown mucilage to 300 ℃ isolated from air, and sinter at 300 ℃ for 3 hours; cool to room temperature, and pulverize into particle size 200 mesh powder precursor; place the powder precursor in Al 2 O 3 In a porcelain boat, the carbon compounds were prepared by sintering at 400 °C for 8 hours in an air atmosphere, and then cooling naturally.
[0039] 2) Preparation of reduced carbon compounds
[0040] Weigh sodium borohydride according to the weight ratio of sodium borohydride t...
Embodiment 3
[0044] 1) Preparation of carbon compounds
[0045] Mix citric acid and ethylene glycol in a molar ratio of 1:4, stir at 60 °C for 2 h, place at 1013Pa and stir at 165 °C for 5 h to carry out the polymerization reaction; vacuum dry at 175 °C under a pressure of 1013Pa, remove those that do not participate in the polymerization reaction. Ethylene glycol, to get brown slime. The brown mucilage was heated to 300 °C in isolation from the air, sintered at 300 °C for 3 h, cooled to room temperature, and pulverized into a powdery precursor with a particle size of 100 mesh; the powdered precursor was placed in Al 2 O 3 In a porcelain boat, the carbon compounds were prepared by sintering at 400 °C for 8 h in an air atmosphere, and then cooling to room temperature naturally.
[0046] 2) Preparation of reduced carbon compounds
[0047] Triethylsilane was weighed at 1:100 in weight ratio of triethylsilane to carbon compound. The triethylsilane solution was prepared by dissolving trieth...
PUM
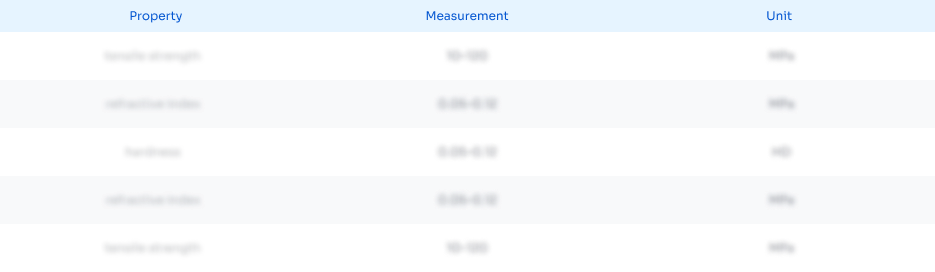
Abstract
Description
Claims
Application Information

- R&D Engineer
- R&D Manager
- IP Professional
- Industry Leading Data Capabilities
- Powerful AI technology
- Patent DNA Extraction
Browse by: Latest US Patents, China's latest patents, Technical Efficacy Thesaurus, Application Domain, Technology Topic, Popular Technical Reports.
© 2024 PatSnap. All rights reserved.Legal|Privacy policy|Modern Slavery Act Transparency Statement|Sitemap|About US| Contact US: help@patsnap.com