Preparation method for acrylonitrile copolymer type water blocking yarns
A technology of acrylonitrile and copolymer, which is applied in the field of preparation of acrylonitrile copolymer water-blocking yarn, which can solve the problems of long-term stability of power cable transmission performance, inability to adapt to high-temperature production environment, and unsatisfactory longitudinal water-blocking effect. Achieve good water blocking effect, good water absorption rate, and good longitudinal effect
- Summary
- Abstract
- Description
- Claims
- Application Information
AI Technical Summary
Problems solved by technology
Method used
Examples
Embodiment 1
[0014] (1) Add 50g of starch and 0.8g of sodium chloride into a mixed solution of 84ml of water and epichlorohydrin and stir, add dropwise 20ml of potassium hydroxide solution with a mass fraction of 10% and react, neutralize the reaction solution with hydrochloric acid, Filter, wash with water and absolute ethanol, and dry to obtain cross-linked starch;
[0015] (2) Add 6ml of ferrous sulfate solution with a mass fraction of 2%, 30ml of acrylonitrile and 5ml of hydrogen peroxide with a mass fraction of 6% in sequence to 150ml of aqueous solution containing 25g of cross-linked starch, and react at 35°C for 1 hour, Aftertreatment obtains powdery acrylonitrile copolymer;
[0016] (3) Dip synthetic fiber filaments in water dispersed with acrylonitrile copolymers, take them out and dry them to obtain acrylonitrile copolymer water-blocking yarns.
Embodiment 2
[0018] (1) Add 23g of starch and 0.5% sodium chloride into a mixed solution of 90ml of water and epichlorohydrin and stir, add dropwise 17ml of potassium hydroxide solution with a mass fraction of 10% and react, neutralize the reaction solution with hydrochloric acid, and filter , washed with water and absolute ethanol, and dried to obtain cross-linked starch;
[0019] (2) Add 6ml of ferrous sulfate solution with a mass fraction of 2%, 28ml of acrylonitrile and 4ml of hydrogen peroxide with a mass fraction of 6% to 150ml of aqueous solution containing 27g of cross-linked starch, and react at 40°C for 1.5 hours. Aftertreatment obtains powdery acrylonitrile copolymer;
[0020] (3) Dip synthetic fiber filaments in water dispersed with acrylonitrile copolymers, take them out and dry them to obtain acrylonitrile copolymer water-blocking yarns.
Embodiment 3
[0022] (1) Add 78g of starch and 1.5g of sodium chloride into a mixed solution of 134ml of water and epichlorohydrin and stir, add dropwise 32ml of potassium hydroxide solution with a mass fraction of 10% and react, neutralize the reaction solution with hydrochloric acid, Filter, wash with water and absolute ethanol, and dry to obtain cross-linked starch;
[0023] (2) Add 7ml of ferrous sulfate solution with a mass fraction of 2%, 33ml of acrylonitrile and 7ml of hydrogen peroxide with a mass fraction of 6% to 150ml of aqueous solution containing 27g of cross-linked starch, and react at 45°C for 2 hours. Aftertreatment obtains powdery acrylonitrile copolymer;
[0024] (3) Dip synthetic fiber filaments in water dispersed with acrylonitrile copolymers, take them out and dry them to obtain acrylonitrile copolymer water-blocking yarns.
[0025] According to the preparation method of the acrylonitrile copolymer water-blocking yarn disclosed in the present invention, the obtained a...
PUM
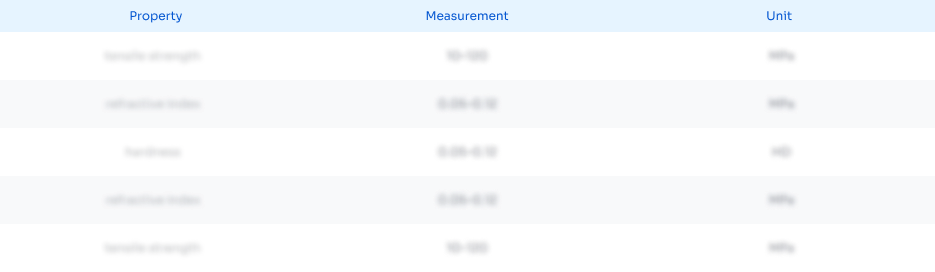
Abstract
Description
Claims
Application Information

- R&D
- Intellectual Property
- Life Sciences
- Materials
- Tech Scout
- Unparalleled Data Quality
- Higher Quality Content
- 60% Fewer Hallucinations
Browse by: Latest US Patents, China's latest patents, Technical Efficacy Thesaurus, Application Domain, Technology Topic, Popular Technical Reports.
© 2025 PatSnap. All rights reserved.Legal|Privacy policy|Modern Slavery Act Transparency Statement|Sitemap|About US| Contact US: help@patsnap.com