Integrated gas retort
A retort furnace and an integrated technology, applied in the direction of indirect heating retort, coke oven, petroleum industry, etc., can solve problems such as difficult and poor uniform gas distribution of retort furnaces, and reduce construction costs, energy consumption and operating costs , the effect of reducing the load
- Summary
- Abstract
- Description
- Claims
- Application Information
AI Technical Summary
Problems solved by technology
Method used
Image
Examples
Embodiment Construction
[0041] attached image 3 It is a flow chart of the integrated dry distillation process. The figure shows that the integrated dry distillation process does not set an independent heating furnace. After the dry distillation gas is discharged from the dry distillation furnace, the shale oil is recovered by the oil recovery device, and is cooled to 35 ° C ~ 40 ° C, and enters the gas cabinet. A part is directly sent to the combustion chamber of the integrated carbonization furnace by the gas fan as fuel; a part is sent to the bottom of the integrated carbonization furnace by the gas fan to recover the waste heat of the semi-coke, and the temperature rises above 450 ° C and merges with the carbonization oil gas to pre-process the material. Heat drying, the temperature of the retort gas keeps dropping during the rising process, and the temperature at the outlet of the retort furnace is about 90°C to 110°C, and then it is introduced into the oil recovery system to collect oil, and th...
PUM
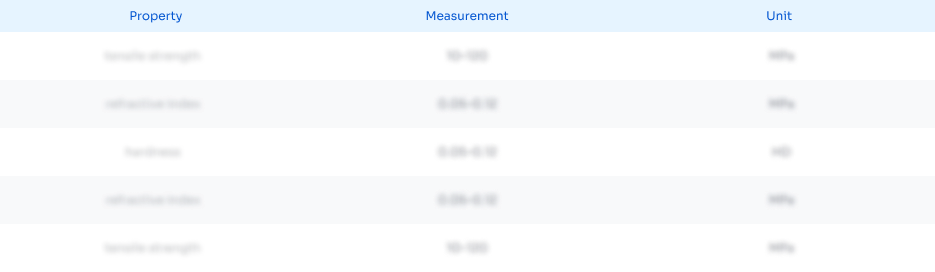
Abstract
Description
Claims
Application Information

- Generate Ideas
- Intellectual Property
- Life Sciences
- Materials
- Tech Scout
- Unparalleled Data Quality
- Higher Quality Content
- 60% Fewer Hallucinations
Browse by: Latest US Patents, China's latest patents, Technical Efficacy Thesaurus, Application Domain, Technology Topic, Popular Technical Reports.
© 2025 PatSnap. All rights reserved.Legal|Privacy policy|Modern Slavery Act Transparency Statement|Sitemap|About US| Contact US: help@patsnap.com