Technique for recovering hydrogenated nitrile-butadiene rubber
A technology of hydrogenated nitrile butadiene rubber and process, which is applied in the technical field of restoring hydrogenated nitrile butadiene rubber, can solve the problems of low physical properties, high price, difficult regeneration of hydrogenated nitrile butadiene rubber, etc., and achieve simple process, excellent effect and recovery of plasticity Effect
- Summary
- Abstract
- Description
- Claims
- Application Information
AI Technical Summary
Problems solved by technology
Method used
Image
Examples
Embodiment 1
[0016] The invention as figure 1 Shown: using waste and old hydrogenated nitrile rubber as raw material, it is prepared by sequentially including cleaning, grinding, impurity removal, recovery reaction and mixing process.
[0017] The restoration reaction comprises dropping into the restoration agent of 2.5% by weight in the raw material;
[0018] The recovery agent is composed of zinc diethyldithiocarbamate, mercaptobenzothiazole and zinc oxide, and the weight ratio of the three is: 2.3:1.8:1;
[0019] The kneading process uses a kneader, and kneads for 48 minutes in an environment of 18°C.
[0020] The manufacturing process of the restoring agent is as follows: adding zinc diethyldithiocarbamate, mercaptobenzothiazole and zinc oxide into 20 parts by weight of dibasic alcohol solution, and then distilling.
[0021] The raw material was ground to 40 mesh.
Embodiment 2
[0023] The invention as figure 1 Shown: using waste and old hydrogenated nitrile rubber as raw material, it is prepared by sequentially including cleaning, grinding, impurity removal, recovery reaction and mixing process.
[0024] The recovery reaction comprises dropping into the recovery agent of 1.5% by weight in the raw material;
[0025] The recovery agent is composed of zinc diethyldithiocarbamate, mercaptobenzothiazole and zinc oxide, and the weight ratio of the three is: 2.7:2.2:1;
[0026] The kneading process uses a kneader, and kneads for 28 minutes in an environment of 30°C.
[0027] The manufacturing process of the restoring agent is as follows: adding zinc diethyldithiocarbamate, mercaptobenzothiazole and zinc oxide into 20 parts by weight of dibasic alcohol solution, and then distilling.
[0028] The raw material was ground to 100 mesh.
Embodiment 3
[0030] The invention as figure 1 Shown: using waste and old hydrogenated nitrile rubber as raw material, it is prepared by sequentially including cleaning, grinding, impurity removal, recovery reaction and mixing process.
[0031] The restoration reaction comprises dropping into the restoration agent of 2% weight ratio in the raw material;
[0032] The recovery agent is composed of zinc diethyldithiocarbamate, mercaptobenzothiazole and zinc oxide, and the weight ratio of the three is: 2.5:1.95:1;
[0033] The kneading process uses a kneader, and kneads for 32 minutes in an environment of 25°C.
[0034] The manufacturing process of the restoring agent is as follows: adding zinc diethyldithiocarbamate, mercaptobenzothiazole and zinc oxide into 20 parts by weight of dibasic alcohol solution, and then distilling.
[0035] The raw material was ground to 60 mesh.
[0036] Further explain the present invention below:
[0037] In general, the present invention adds a chemica...
PUM
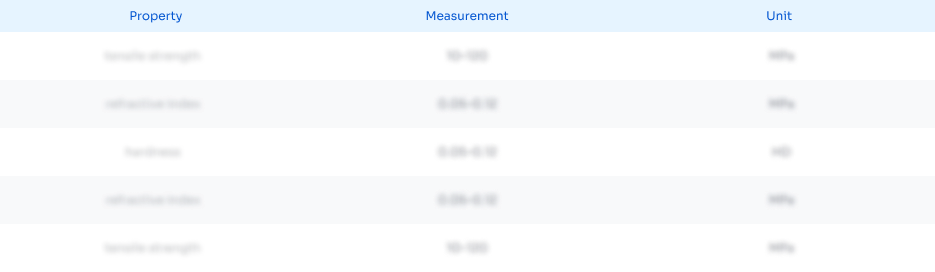
Abstract
Description
Claims
Application Information

- R&D
- Intellectual Property
- Life Sciences
- Materials
- Tech Scout
- Unparalleled Data Quality
- Higher Quality Content
- 60% Fewer Hallucinations
Browse by: Latest US Patents, China's latest patents, Technical Efficacy Thesaurus, Application Domain, Technology Topic, Popular Technical Reports.
© 2025 PatSnap. All rights reserved.Legal|Privacy policy|Modern Slavery Act Transparency Statement|Sitemap|About US| Contact US: help@patsnap.com