Grooving method for multi-wire cutting of super-thick products by aid of guide wheels
A technology of multi-wire cutting and slotting method, which is applied in the direction of fine working devices, stone processing equipment, manufacturing tools, etc., can solve the problems of limited product varieties, jumping wires, and inability to process, and achieve the effect of expanding product capabilities
- Summary
- Abstract
- Description
- Claims
- Application Information
AI Technical Summary
Problems solved by technology
Method used
Image
Examples
Embodiment 1
[0016] For example, to cut a product with a thickness of 8mm, set the groove distance P = 8mm, and the system consists of 4 guide wheels. Using this method, first determine the distance A between the first groove of the first guide wheel and the reference plane of the guide wheel as 5mm; then the first The distance between the first groove of the 2 guide wheels and the reference surface of the guide wheels B=A+(C-1)+P / N=5+(2-1)*8 / 4=7mm; the first of the third guide wheel The distance between the groove and the reference plane of the guide wheel is B=9mm; the distance between the first groove of the fourth guide wheel and the reference plane of the guide wheel is B=11mm. In this way, the steel wire on each guide wheel will form a small angle (about 0.27°) with the wire groove, which avoids the occurrence of jumping wires.
PUM
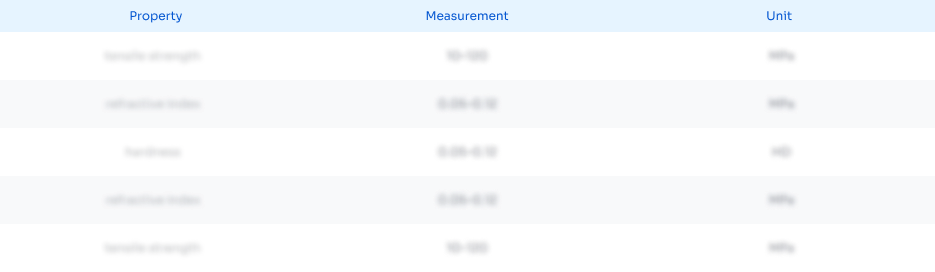
Abstract
Description
Claims
Application Information

- R&D Engineer
- R&D Manager
- IP Professional
- Industry Leading Data Capabilities
- Powerful AI technology
- Patent DNA Extraction
Browse by: Latest US Patents, China's latest patents, Technical Efficacy Thesaurus, Application Domain, Technology Topic, Popular Technical Reports.
© 2024 PatSnap. All rights reserved.Legal|Privacy policy|Modern Slavery Act Transparency Statement|Sitemap|About US| Contact US: help@patsnap.com