Method for manufacturing calcium metal core-spun yarn of high purity
A manufacturing method and metal calcium technology, applied in the field of steelmaking, can solve the problems of secondary pollution of molten steel, large loss of calcium, low absorption rate, etc., and achieve the effects of sufficient molten steel treatment, delayed calcium melting, and high calcium absorption rate
- Summary
- Abstract
- Description
- Claims
- Application Information
AI Technical Summary
Problems solved by technology
Method used
Examples
Embodiment Construction
[0026] The manufacturing method of the high-purity metal calcium cored wire of the present invention includes the following process steps:
[0027] (1) Purification of metallic calcium into metallic calcium rods (wires) or core particles: use vacuum melting and casting equipment to heat and melt the metallic calcium in a vacuum furnace to 850℃~1000℃ for reduction and purification, and then the purity is greater than 99% Calcium metal is vacuum cast, and the finished product is cast into a calcium rod (wire) with a diameter of 80-100mm and a length of 400-500mm; it is made into a calcium rod.
[0028] (2) Metal calcium core passivation and sealing: passivate the metal calcium core to isolate the metal calcium core from air and prevent oxidation;
[0029] (3) Coating and shaping of the steel strip wrapped with calcium metal core: the inner surface of the steel strip wrapped with calcium metal core is coated with high-temperature gasification materials, and a preliminary preliminar...
PUM
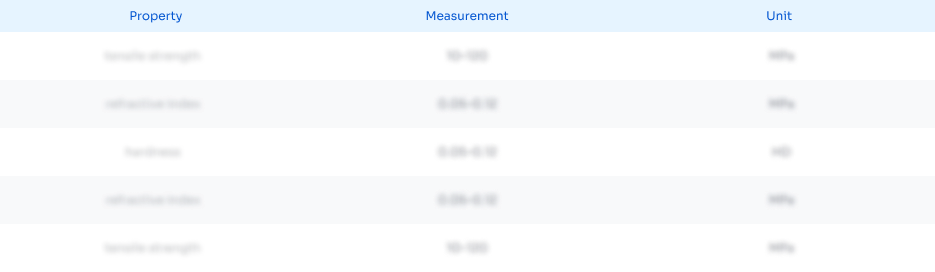
Abstract
Description
Claims
Application Information

- R&D
- Intellectual Property
- Life Sciences
- Materials
- Tech Scout
- Unparalleled Data Quality
- Higher Quality Content
- 60% Fewer Hallucinations
Browse by: Latest US Patents, China's latest patents, Technical Efficacy Thesaurus, Application Domain, Technology Topic, Popular Technical Reports.
© 2025 PatSnap. All rights reserved.Legal|Privacy policy|Modern Slavery Act Transparency Statement|Sitemap|About US| Contact US: help@patsnap.com